平準化とは?量の平準化と種類の平準化の違いを解説
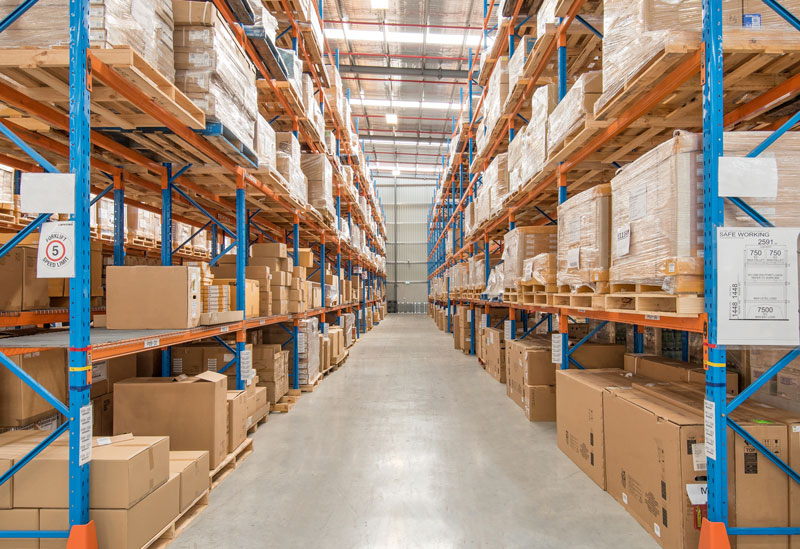


平準化(へいじゅんか)とは
2種類の平準化
本ページでは、平準化とは何か、2種類の平準化について、その概要とポイントを解説しています。
平準化とは、平らにならして生産を行なうことを指します。平準化には2種類あります。
2種類の平準化というのは、量の平準化と種類の平準化です。この2つを混同している人が沢山います。新人や部下に聞かれた際に、正しく説明できるレベルを目指しましょう。
1つは、「量」の平準化です。量の平準化とは、生産量、あるいは、生産数、生産時間等を、ある一定の区間内において、一定のボリュームにして生産を行なうことを指します。
もう1つは、「種類」の平準化です。種類の平準化とは、複数の品種の生産を行なう際、品種毎にまとめて流すのではなく、万遍なくバラシて生産を行なうことを言います。
それぞれについて詳細を確認していきましょう。
量の平準化とは
量の平準化とは、生産量、あるいは、生産数、生産時間等を、ある一定の区間内において、一定のボリュームにして生産を行なうことです。当然のことながら、どんな製品の注文でも、お客様からの注文量は毎日、毎週、毎月バラバラです。このバラツキにどうやって対応していくかが、非常に重要な生産課題となります。
一般に、お客様からの注文量のバラツキをそのまま生産計画へ反映させると、日々生産量が大きくバラツクことになります。そうなった場合、生産側は、どうしても「生産が最大な時に必要な人員を抱えていく」という対応になってしまいます。そのことにより、生産が少ない場合は過剰人員による手待ちロス等が発生することになるのです。
従って、基本的には、月単位で平準化して生産を実施していきます。その月の生産数に応じた工数(=人員)を確保し投入していくという対応を行ないます。お客様の注文のバラツキに答えるという視点と、ロスを発生させずに効率よく生産を行なうという視点の2つをバランスよく持ち、生産体制を構築していくことが必要不可欠であることを覚えておきましょう。
種類の平準化とは
種類の平準化とは、複数の品種の生産を行なう際、品種毎にまとめて流すのではなく、万遍なくバラシて生産を行なうことを言います。種類の平準化を行なわないことにより、大きく3つの問題が発生します。
1つ目:製品在庫が増加し、お客様が欲しい時に供給できない
2つ目:前後工程の生産負荷に大きなバラツキが発生する
3つ目:サプライヤーの対応が不安定になる
種類の平準化を行なわないと、リードタイムの悪化や部品価格の上昇、コスト増加へ繋がってしまい、結局は競争力が低下してしまいます。このような状況にならないためにも、種類の平準化という考え方を、しっかりと理解しておきましょう。


平準化の必要性
平準化生産とは
平準化生産とは、平均化した水準で生産をすること
平準化生産とは、平均化した水準で生産をすることです。この平準化生産はジャストインタイムの前提条件となり、マーケットインでお客様のニーズに応えるためには必須の考え方となります。
マーケットインとは
ここで、マーケットインについて補足をします。マーケットインとは、何のことでしょうか。それは、市場や買い手の立場に立って、必要とするモノを提供していくことです。
一番重要なことは、自社の商品が選ばれることです。
そのために、欲しい製品を、欲しい時に、お客様が求める価格で提供して行こうという考え方です。欲しい製品というのは、必要な機能、欲しい機能を持つ製品のことを言います。欲しい時にというのは、ジャストインタイムで、ということです。お客様が求める価格でというのは、対価として払ってもよいと納得できる価格でということです。
当然のことですが、お客様はムダから発生するコストには、1円たりともお金を払いたくないと思っています。従って、製品、商品をつくる上では、ムダを徹底的に排除していくことが不可欠なのです。
平準化が出来ていないと・・・
平準化が出来ていないことにより発生する問題は下記の通りです。
- 人員計画に遊び(ムダ)が発生し、コストアップに繋がる
- 在庫が発生し、管理コストが増大する
- 製造リードタイムが延び、お客様の ニーズに応えれない
- 基準工程以外の生産負荷がバラツいてしまい、遅れや遊びが発生する
- サプライヤーが対応できず、部品納入遅れの発生や価格アップに繋がる
なお、究極は、1個単位にまで生産を平準化することではあるものの、段取り替えの増加などの課題も多く、決して簡単ではありません。自社の実力をしっかりと見極め、少しずつ実力を上げながら平準化のレベルも上げていくことが大切です。
量の平準化を考えないとどうなる?
量の平準化を全く考えずに生産をすると、人員は生産量が多い時に合わせて配置をしなければいけなくなります。例えばスライドの例では、最少5人、最大10人の負荷ですが、月を通して10人の人員計画を組まざるを得ない状態です。これでは当然遊びが発生してしまいます。
一方で、量の平準化を行なうと、月を通して7人が必要人員であり、遊びが発生することはありません。この例だと配置人員の差は3人であり、明らかに違いが出ることがわかると思います。
一般的に、人員計画は、月単位で変更するのが妥当な対応です。無暗に 日々のバラツキを吸収しようとすると、遊びが発生してしまい、付加価値を生まない労務費の増加によるコストアップに直結します。月内の負荷を100%平準化することは、当然至難の業ですが、この考えを念頭に置いて、なるべく負荷のバラツキが起こらないような生産計画の作成を目指していきましょう。
量の平準化未実施の負のスパイラル
では、おさらいとして、量の平準化の負のスパイラルを確認していきましょう。
まず、量の平準化の未実施により、遊びや手待ちによるムダが発生します。そして、そのムダにより、付加価値を生まない時間が増加、つまり労務費が増加します。この労務費の増加は販売価格の上昇、あるいは利益の減少に繋がります。そして、最終的には、競争力の低下に繋がっていくという、負のスパイラルに陥っていきます。
このような状況にならないためにも、量の平準化という考え方をしっかりと理解しておきましょう。
種類の平準化を考えないとどうなる?
種類の平準化が出来ていないと、次の3つの問題点が発生することを冒頭に述べました。それぞれ詳細について確認していきましょう。
1つ目:製品在庫が増加し、お客様が欲しい時に供給できない
2つ目:前後工程の生産負荷に大きなバラツキが発生する
3つ目:サプライヤーの対応が不安定になる
1つ目:製品在庫が増加し、お客様が欲しい時に供給できない
まず、製品在庫が増加し、お客様が欲しい時に供給できないことについて、車の組立を例に取り説明します。
大前提として、上の絵のように、お客様からの注文は各種類、バラバラに入ってきます。それを、スライドの下の絵のように、ダンゴ生産をしてしまうとどうなるのか、考えてみましょう。
赤い矢印は、お客様が欲しい時に供給できていないことを線で表しています。例えば、青い車が欲しい場合でも、この場合初めに黄色の車を続けて造るため、後半の青の車の生産までお客様は待たなければいけません。
そして、青い矢印は、お客様の注文の前に造らなければならないことを表しています。例えば、初めに黄色い車をまとめて造らなければいけないため、まだ注文が入っていなくても、見込みで造らなければいけません。
これは製品在庫の発生や、売れ残りのリスクの発生に繋がってしまいます。少々極端な例ですが、基本的にはダンゴ生産は、お客様のニーズとは全く逆の対応となってしまうのです。
では平準化生産を行なう場合はどうでしょうか?先ほどと同じように赤と青の線を引いてみましょう。一目見ただけで違いが分かったと思います。ダンゴ生産から平準化生産を行なうだけで、お客様のニーズへの対応力が大幅にアップし、そして圧倒的に製品在庫も少なくなります。
このことが、種類の平準化の1つ目のメリットです。
2つ目:前後工程の生産負荷に大きなバラツキが発生する
2つ目の、前後工程の負荷のバラツキについて、先ほどと同じ、車を例に取って説明します。例として、黄色、赤、青の車の組立時間は20秒で同じであるものの、鍛造、鋳造のサイクルタイムが表のように異なると仮定しましょう。
まずは、ダンゴ生産の場合です。組立工程の負荷は一定になりますが、この時の前工程の、鍛造、鋳造工程の負荷はどうなるでしょうか。
表の数字で計算すると、鍛造工程と鋳造工程は、このように、最大で2倍もの大きな負荷のバラツキが発生します。
では一方で、平準化生産の場合はどうなるでしょうか。
この例の場合だと、先ほどのダンゴ生産の場合と比較して、バラツキは20から10へ減少しました。もうお分かりのように、平準化生産では、前後工程の負荷のバラツキが低減するという効果があります。これが2つ目のメリットです。
3つ目:サプライヤーの対応が不安定になる
3つ目の、サプライヤーの対応が不安定になることについても、同じく車を例に取って説明します。簡略化の為、黄色の車はサプライヤー A、赤色の車はサプライヤー B、青色の車はサプライヤー Cからのみ部品が供給されると仮定しましょう。
では、ダンゴ生産の場合、サプライヤー Aでは、どのような 問題が発生するでしょうか。
平準化をしないとサプライヤーでは2つの問題が発生します。
サプライヤーAでは2つの問題が発生します。
1つ目は、必要なタイミングで必要な分の部品を造るには、生産力に余剰を持っておかなければいけないこと。2つ目は、生産力に余剰を持たずに、ジャストインタイムで供給する為には、在庫を沢山持って対応しなければいけないことです。
自動車会社での組立工程で平準化を行なわないことにより、サプライヤーでは生産力の余剰や、在庫を持つムダが発生するのです。このムダは、結局はコストアップへ繋がってしまいます。
最終組立工程が平準化生産を行なうことでコストダウンに
一方で、自動車組立工程が平準化すると、このように、必要なタイミングで造り、すぐに供給すればよくなります。
以上のように、最終組立工程が平準化生産を行なうことで、サプライヤーは余剰能力や在庫を持たずに、ジャストインタイムで生産・供給ができるようになります。
これが部品のコストダウンに繋がり、完成車メーカーも顧客ニーズへの対応力がアップし、競争力向上に繋がっていくのです。
種類の平準化を行なわない場合に起こる負のスパイラル
おさらいとして、種類の平準化を行なわない場合に起こる、負のスパイラルを確認しましょう。
種類の平準化を行なわないと、部品の必要タイミングにバラツキが発生します。そして、そのバラツキにより、サプライヤーの納入遅れの増加や生産負荷のバラツキ、在庫の発生などの問題が生じます。これらの問題は、リードタイムの悪化や部品価格の上昇、コスト増加へ繋がります。そして、最終的には、競争力の低下に繋がっていく、という負のスパイラルに陥っていきます。
このような状況にならないためにも、種類の平準化という考え方を、しっかりと理解しておきましょう。


量の平準化と種類の平準化のまとめ
以上で学んだことをまとめてみましょう。
かんばんとは?かんばんの役割や種類、基本ルールとは?
- 平準化とは、平らにならして生産を行なうこと
- 平準化には、量の平準化と種類の平準化の2種類がある
- 量の平準化をしないと、人員計画に遊び(ムダ)が発生し、コストアップに繋がる
- 種類の平準化をしないと、在庫が発生し、管理コストが増大する
- また、製造リードタイムが延び、お客様のニーズに応えれなくなる
- 基準工程以外の生産負荷がバラツいてしまい、遅れや遊びが発生する
- サプライヤーが対応できず、部品納入遅れの発生や、価格アップに繋がる
いかがでしたか?本ページでは、平準化の種類や平準化を行なわなければいけない理由について解説しました。
ジャストインタイム生産のレベルを上げるために、2つの平準化のレベルを上げていきたいですね!


「平準化」に関する教材ダウンロード
無料会員に登録すると教材のダウンロードができます!
ダウンロードした資料につきましては、コンテンツ利用規約に同意の上、ご利用くださいますようお願い致します。例えば、下記の行為は禁止となります(利用規約を一部抜粋)
- 本コンテンツを利用してのコンサルティング業務をする行為
- 利益享受または販売を目的として利用(販売やWEBサイトへの掲載等)をする行為
- 二次的著作物を制作し第三者に配布する行為
- 弊社または第三者の財産、名誉、プライバシー等を侵害する行為
使用用途 | 社内教育や発表資料作成における作業効率化等 |
---|---|
ファイル形式 | PowerPoint |
教材ダウンロード | 無料会員に登録すると、ココにダウンロードボタンが表示されます。 |
ログイン/無料会員登録はこちらから
無料会員/有料会員の方はログインしてください。
新規会員登録のご案内
会員登録特典!
- 閲覧できる動画が2倍に増加
- カイゼン講座で使用している資料の一部がダウンロード可能
- 実務で使えるテンプレートがダウンロード可能
- カイゼン情報や限定情報満載のメルマガが受け取れる
個人向け有料動画サービスに申し込むと、さらに充実!
限定の学習動画が閲覧可能になります!
※個人向け有料動画サービスのお申込みには、無料会員登録後、動画配信システムVimeoのお申込みが必要です。
お申込み手順はこちら

関連学習動画
-
k1-01
アニメで学ぶ"カイゼン活動"
有料サービス限定
3:カイゼンの2種類のアプローチ
受講対象者
生産部門全般(新入社員/一般)- カリキュラム構成
-
- カイゼンの2種類のアプローチとは
- 問題発生型カイゼンと課題発生型カイゼン
- 2種類のカイゼンアプローチの必要性
- カイゼンアプローチ別問題解決のステップ
- まとめ
-
k1-01
アニメで学ぶ"カイゼン活動"
有料サービス限定
8:カイゼンマインドを育てる4つの“機会”
受講対象者
生産部門全般(新入社員/一般)- カリキュラム構成
-
- カイゼンマインドを育てる4つの機会
- 4つの機会とは
- 4つの機会とボトムアップ力
- まとめ
-
k1-01
アニメで学ぶ"カイゼン活動"
無料会員限定
2:カイゼンは誰のため?
受講対象者
生産部門全般(新入社員/一般)- カリキュラム構成
-
- 積極的なカイゼン活動チームにするには
- なぜカイゼン活動を行うのか
- カイゼンは自分のため
- それぞれのカイゼンメリットとは
- まとめ
-
k1-01
アニメで学ぶ"カイゼン活動"
有料サービス限定
6:PDCAサイクルとは
受講対象者
生産部門全般(新入社員/一般)- カリキュラム構成
-
- PDCAサイクルとは
- PDCAサイクルのポイント
- よくある失敗事例
- まとめ
-
k1-01
アニメで学ぶ"カイゼン活動"
有料サービス限定
5:ものづくりの3要素「QCD」とは
受講対象者
生産部門全般(新入社員/一般)- カリキュラム構成
-
- ものづくりにおける3つの大事な要素
- QCDとは
- QCDの優先順位
- 安全性の重要性
- まとめ
-
k1-01
アニメで学ぶ"カイゼン活動"
有料サービス限定
7:トップダウンとボトムアップ活動
受講対象者
生産部門全般(新入社員/一般)- カリキュラム構成
-
- トップダウンとは、ボトムアップとは
- カイゼン活動におけるそれぞれの視点
- 結果を出すカイゼン活動を支える有効な視点とは
- まとめ