ムダ取りフレームワークを使ったムダ発想法を身に付けよう!
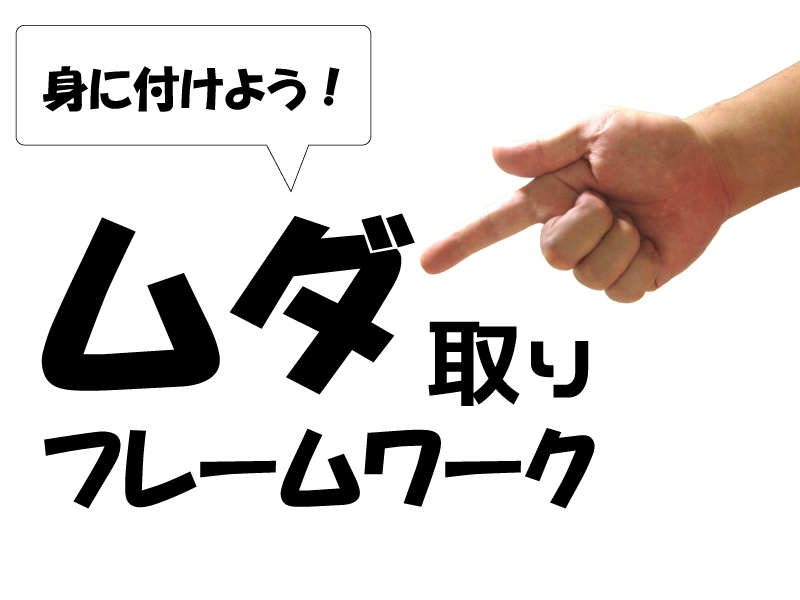


ムダ取りフレームワークを活用してムダを見つけていく視点について解説
ムダを見つけるにはどう発想すればよい?
「ムダ取り」という言葉を聞くと、何を思い浮かべますか?
恐らく、“動きに関するムダ”を取るというイメージを持っている方が多いのではないでしょうか?
しかし、当然ですがそれはムダ取りの一側面でしかありません。
日常の改革・改善活動においてムダを見つける時、現場の管理者から次のような発言聞くことがあります。
「何でもいいから気付いたことを挙げてみて。何でもいいのであればいくらでも挙げられるでしょう!」
これでは少し指示が雑ですよね。受け手からすると、「何でもいいから」と言われると逆に浮かばなくなってしまうのです。
人間は制約が大きいとアイデアや気付きが出にくくなりますが、逆に真っ白な状態で「考えろ」と言われても発想できない生き物です。
これはムダ取りを行なう際にも同様です。
ムダ取りフレームワークを活用しよう!
そこで有効になるのがムダ取りフレームワークです。
例えば、製造現場に着目すると、代表的なものには次のような視点が挙げられます。
作業環境の視点
「日頃の不満」「作業姿勢」「3M(ダラリ)」「照度・休憩・温度等の環境」等の働く場所や環境の悪さがムダを引き起こしていないかという視点からムダを発想するフレームワーク
作業動作の視点
「手作業のムダ」「レーティングのムダ」「思考、体の動き、環境面」「動線のムダ」「動作経済の原則」「ECRSの原則」等、人の動きの基準に対して実情が乖離していないかという視点からムダを発想するフレームワーク
生産の仕組みという視点
「5Sの視点」「スペース効率の視点」「ラインバランスの視点」「人員配置の視点」等、そもそもの生産の仕組みの基本に対して実情が乖離していないかという視点からムダを発想するフレームワーク
7つのムダの視点
トヨタ生産方式における7つのムダの視点も有効です。加工、在庫、造りすぎ、手待ち、動作、運搬、不良・手直しの視点からムダを定義しています。
7つのムダに関しては、下記のページで詳細を解説しています。
[reg-bnr]7つのムダとは ムダの定義 ムダとは、顧客にとって価値のある作業や業務(付加価値)以外の全てのもののことです。 日々の作業や業務は、それを行なう側から見ると、「自分達にとって必要な作業」と「自分達にと...
フレームワークは気付きの連鎖を生むきっかけになる
更に、これらのフレームワークを学ぶことで、「そんなムダがあるならこれもムダと言っていいよね。」というような、気付きの連鎖も生まれやすくなるのです。
現場改善コンサルタントと呼ばれる人物は、実はこのような視点や基準を頭の中に叩き込んでいます。現場を巡回した時には、その基準と比較して「あれ?これは劣っているな。」「これは何か違和感を覚えるな。」といった感覚をもとに指導をしていきます。
つまり、しっかりと基本となるフレームワークを身に付けておくことで、コンサルタントなんかいなくてもムダ取り活動を進めることができるようになります。
本ページでは、ムダを見つけるフレームワークについて、弊社の学習コースから一部を抜粋して解説しています。


ムダとは何か?ムダ取りの必要性とは
ムダとは
それでは早速、ムダとは何か確認していきます。
ムダとは何か答えられますか?
ムダとは何かと聞かれた時、答えることはできますか?
ムダとは、“付加価値”を付けていること以外の全てのことです。
自分達がどのくらい頑張っているか、どのくらい時間を掛けているかには関係なく、「付加価値」を付けているかいないかが大切な視点となります。
顧客視点のムダも含めて考えよう
一般に、ムダは何かと問われると、その職場にとって必要か不要かで判断されることが多いと思います。
自分達にとって必要のないものがムダであり、顧客に価値を提供するために必要な仕事はムダではないと考えてしまうのです。
しかし、この基準ではムダの全てを表現するには正しくないと言わざるを得ません。どういうことなのでしょうか。
視点を変えて、「顧客にとって価値のある作業」は何かと考えてみましょう。顧客の視点から見ると、顧客にとって価値のある作業と、顧客にとって価値のない作業に分けられます。この図からお分かりの通り、多くの場合、自分達にとって必要な作業と、顧客にとって価値のある作業は、全く同じではありません。
顧客にとって価値のある作業かつ自分達にとって必要な作業は、付加価値と呼ばれるものです。いかにこの付加価値を高めていくかが現場では必要不可欠な視点となります。一方、顧客にとって価値がない作業で、組織にとって必要のないものは、明らかなムダと呼ばれます。いかにこのムダを減らしていくかが大切です。
そして、自分達にとって必要であったとしても、顧客にとって価値があると思ってもらえない作業があります。
さてこれは、付加価値でしょうか、ムダでしょうか?
実はこれは、顧客視点のムダと呼ばれ、ムダに分類されます。例えば、製品を10回運搬しても、100回運搬しても、顧客から見たら知ったことではないのです。
顧客から価値があると言ってもらえないものは、ムダとして認識しなければいけないのです。
つまり、ムダとは何かを考える時、自分達の目線だけでなく顧客目線でムダを認識することが非常に大切な考え方となります。この認識がないと、ムダをムダとして見ることが出来なくなってしまい、いつも自分達の都合だけで物事を捉えるようになってしまいます。しかし、あくまで企業は、顧客が求める「付加価値」に対して対価としてお金を受け取っていることを忘れないようにしましょう。
ムダ取りはなぜ必要なのか
それでは次に、「ムダ取りはなぜ必要なのか」について考えてみましょう。
販売金額は造る側の考えだけで決められない
まずは大前提として覚えておかなければいけないことがあります。それは、基本的に販売金額は、顧客のニーズによって決まる、つまり造る側の考えだけで決められないということです。
自社都合で変えるのが難しい販売金額(お客様から頂くお金)の内訳を見てみましょう。
材料費等の外部購入価値と呼ばれるものと、各種コストと利益で構成されます。このうち、材料費等と各種コストを合計したものが総原価と呼ばれます。
さてここで質問です。緑色の部分で表している利益を増やすためには、どうしたらよいでしょうか?可能性のある選択肢を3つ挙げてみましょう。
ヒントは、販売金額、総原価をどうすればよいのかという視点です。
利益を増やす3つのパターン
利益を増やす可能性のあるのは、基本的にはこの3つだけです。
「販売金額を上げる」「総原価を減らす」「その両方を行なう」
販売価格を上げたら売上が減ってしまうリスクも
ただし、販売金額を上げるという選択肢は、簡単にできるものではありません。なぜならば、市場動向にも左右されるため、沢山売ろうと思っても思うように売れないことも多々あるからです。
また、安易に販売価格を上げたら売上が減ってしまうリスクも生じてしまいます。
総原価を減らす方向性が非常に大切
従って、総原価を減らす方向性が非常に大切となります。
そのためにムダ取りを行なわなければならないのです。
総原価を減らして利益を上げる
当たり前のことではありますが、総原価が増加し、販売価格を超えてしまったら赤字に転落します。
これとは逆に、総原価を減少させることができれば、利益が増加し企業の儲けが向上するのです。「総原価を減らして利益を上げる」ことがムダ取りが必要な理由の1つであると覚えておきましょう。
総原価、製造原価とは?
それではここで、総原価にはどんなものが含まれるのか、主なものを挙げてみましょう。
総原価を大きく分類すると、売るのに掛かるお金と、造るのに掛かるお金があります。
売るのに掛かるお金には、「営業に関わる人の人件費」「CM等の広告費」「販売のための交通費」等が挙げられます。
作るのに掛かるお金には、「造ってくれた人の人件費」「造るのに必要な材料代」「電気代、ガス代」等が挙げられます。
作るのに掛かるお金は、製造原価と呼ばれ、工場ではこれを継続的に下げることが求められるのです。
ムダ取りで重要な製造原価の内訳
ここまでの内容を整理してみましょう。
まず、販売金額(売上)の内訳を見ると、造って売るのに掛かったお金である「総原価」と利益に分けられます。
そして、総原価は、造るのに掛かったお金である「製造原価」、売るのに掛かったお金である「販売費」、営業外費用に分けられます。
さらに、ムダ取りで重要な製造原価は、造る人に掛かるお金である「直接労務費」、造るための材料に掛かるお金である「直接材料費」、電気代、ガス代のお金等の「直接経費」、製造間接費に区分されます。
このような体系図を見ると、どうすれば利益が増えるのかは分かりますよね!ムダを取ることで、継続的に労務費・材料費・経費を削減し、そして利益を増やすことが企業には求められるのです。
会社の利益は社員全員に直接関係している
以上のように、利益は製品を造る・売るのに関係した全ての人が関わって生まれています。
つまり、会社の利益は社員全員に直接関係しているのです。
そして、生まれた利益は、将来へ投資されます。例えば、
・給料やボーナスアップによる社員のモチベーション向上
・設備の新設・更新による、使いやすさと生産能力向上
等が代表的な投資の例となります。
ムダ取りは、顧客満足度向上、社員満足度向上、離職率低下等、あらゆる面に効果があると覚えておきましょう。
ムダが生まれる要因
それでは次に、「ムダが生まれる要因」について確認します。
ムダは2つの要因から生まれる
ムダは何から生まれると思いますか?実は、次の2つから生まれると言われています。
1つは、先入観、もう1つは、無知です。
先入観とは、「きっとこうに違いない」「今が一番効率がいいはずだ」「自分にムダがあるわけがない」というような思い込みのことを指します。先入観を意識的・無意識的に持っていることで、ムダを生んでしまい、ムダに気付くことができなくなります。
無知とは、「何がムダか分からない」「ムダの見つけ方を知らない」「もっといいやり方を知らない」ことを指します。ムダを知らないため、ムダがあるか分かっていない、あるいは分かっていてもどう表に出してよいか分からない状態なのです。
先入観によりムダはないと思い込んでいる
例えば、こんなことはないでしょうか。
「何年も前からこの方法で作業を行なっているからムダではないはずだ」と言っているのにも関わらず、なぜその工程があるのか、その工程を止めたらどうなるのかと問うと、「そう言われると答えられない」というケースです。
実は不要だった、というのはよくある話なのです。先入観により、ムダはないと思い込んでいることで、本来簡単に気付けるはずのムダに気付いていない、ということは案外多いものだと思っておきましょう。
ムダを無くすためには、まずはムダを見つけることが必要
ムダを無くすためには、まずは、ムダを見つけることが必要です。必要かどうかで物事を見ていても、顧客のムダを見つけることは難しいものです。なぜならば、顧客にとって何に価値があるのかが分からないと何がムダか分からないからです。
従って、ムダを無くし利益を創出するために、次の3つのことを意識していかなければなりません。
ムダを無くすために持つべき3つの意識
1つ目は、価値を見る目を養い、ムダに気付く力を付けることです。
2つ目は、ムダを無くし「改善することが仕事の本質」だという意識を持つようにすることです。
3つ目は、過去に捕らわれず常識の壁を破る力を付けることです。
これら3つを意識的に持つようにしてください。
アイデアの創造を阻む3つの壁
そして、アイデアの創造を阻む3つの壁が存在していないかという視点でも自分の職場を見つめてみましょう。
まずは、意識の壁です。
「今が一番と考える」「変化に鈍感」「言われないと動かない」「やれない理由から考える」「目的を理解していない」「手段と目的を混同」「原因と結果を混同」等が挙げられます。
次に、感情の壁です。
「間違ったらバカにされる」「焦ってばかりでゆとりがない」「すぐに諦める」「すぐに否定する」「人の言うことを信じない」「すぐ感情的になる」等が挙げられます。
最後に、文化の壁です。
「変化を嫌う」「型にはめたい、はまりたい」「白黒を早くつけたがる」「協調のし過ぎ」「意見を言えない、聞かない」「知識の有り過ぎ」「知識の無さ過ぎ」等が挙げられます。
これらの中で、1つでも当てはまったら要注意です。早急にこれらの壁を打ち破り、ムダ取り活動を推進する土台をつくっていきましょう。これは当然、トップや管理者の役目となります。
“人”に関するムダの分類
それでは次に、人に関するムダの分類について確認します。
人の動きや方法に関するムダを学習
企業では人・モノ・カネを最大限活用することで利益を得ることが出来ます。
その中で、ムダを大きく分類すると、「人の動きや方法に関するムダ」と「設備や材料に関するムダ」の2つがありますが、本講座では、「人の動きや方法に関するムダ」について詳細を学習していきます。
作業は3つに分類される
ではここで、作業の3分類を確認しておきましょう。全ての作業は、価値作業、付随作業、ムダの3つに分類することができます。
価値作業とは、利益を出す(付加価値に繋がる)作業のことです。形状・性質等、物を変化させる作業が該当し、出来る限り増やしたいものとなります。
付随作業とは、完全にムダではないが、付加価値に直結しない作業のことです。今のやり方では必要な作業となりますが、出来る限り削減したいものとなります。
ムダとは、付加価値に結びつかないため、すぐにでも削減すべき作業のことです。
この中で、付随作業とムダを合わせて「広義のムダ」と呼ばれ、ムダ取り活動の対象となります。
付随、ムダに該当する作業をいかに削減することができるか
なお、それぞれの作業の例を挙げるとこのようになります。
価値作業には、加工や機械操作等が挙げられます。
付随作業には、段取りや測定、記録、清掃等が挙げられます。
ムダには、空歩行、手待ち、チョコ停、不良を作る時間等が挙げられます。
ムダ取り活動では、これらの付随、ムダに該当する作業をいかに削減することができるのかを粘り強く考え実行していくことが求められます。


ムダ取りフレームワーク~作業環境~
作業環境からムダに気付くフレームワークについて
それでは早速、作業環境からムダに気付くフレームワークについて確認していきましょう。
4つのフレームワークからムダを見つけよう!
作業環境からムダに気付くための4つのフレームワークを紹介します。
1つ目は、日頃の不満からムダに気付くフレームワーク、
2つ目は、作業姿勢からムダに気付くフレームワーク、
3つ目は、3M(ダラリ)からムダに気付くフレームワーク、
4つ目は、照度、休憩、温度などの作業環境からムダに気付くフレームワークです。
それぞれについて確認していきましょう。
日頃の不満から
まずは、日頃の不満からムダに気付くフレームワークです。
現場の不満や愚痴は改善のタネ
現場では日々改善を行なっています。少しでも歩留りを良くし、少しでも生産性を向上させようと努力しているのではないでしょうか。一方で、現場に入ってみると、現場からは不満や愚痴がよく出てきます。
ほとんどの手順や作業は、理由があって行なうようになったはずです。しかし、初期にしっかり考えずに問題点が残ったまま始めた作業がそのまま理由もなく続いていることも多々あります。また、いつの間にか状況が変わり、昔は必要だったものの今となっては不要なものがそのまま残っていることもあるのです。担当者が代わってしまうと、更に分からなくなってしまいます。特に属人化された仕事の場合はなかなか表に出てきません。
本人は決まったこと、決められたことをやり続けるのが仕事だと思っているため、そこに疑問を持たずに、全て不満となって現れるのです。このような不満を無くすことは、ムダ取りの王道となります。
よく現れる不満の感情
例えば、次のような不満は現れていないでしょうか。
きついなぁ、重いなぁ、やりにくいなぁ、つかれるなぁ、嫌だなぁ、不便だなぁ。
邪魔だなぁ、イライラするなぁ、いちいち面倒だなぁ、難しいなぁ、熱いなぁ。
暑いなぁ、なんとなく不安だなぁ、しっくりいかないなぁ、退屈だなぁ、腰が痛いなぁ。
1つでも思い当たることがあれば、そこにはムダが隠れていると認識することが大切です。これが日頃の不満からムダを見つけるフレームワークとなります。
作業姿勢の視点から
それでは次に、作業姿勢からムダに気付くフレームワークを確認していきましょう。
たかが姿勢と言っておろそかにしてはいけない
無理な作業姿勢、辛い作業姿勢は、集中力の低下、モチベーションの低下、作業時間のバラツキ発生などの悪影響を引き起こします。
一方、楽な作業姿勢は、疲労が溜まりにくい、作業時間が安定しやすい、精神的な余裕が出来るので、気配りが出来るようになる(問題に気付く余裕が生まれる)といった良い影響が期待されます。
たかが姿勢と言っておろそかにすると、ジワジワとムダの発生に繋がっていくことになると覚えておかなければいけません。従って、楽な姿勢で作業ができるように改善しムダを取っていくことは、生産性に影響する大切な視点となるのです。
検査工程の例で考えてみよう
検査工程の例で考えてみましょう。
作業姿勢が最適化されていないと、検査スピードが2倍の速さを求められた場合、顔や体の動きが大きくなり、焦ってハンドリングも悪くなります。つまりムダが発生してしまうのです。結果的に、ミスばかり増え、検査スピードは上がらないのです。
一方、作業姿勢が最適化されている場合、検査スピードが速くなったとしても、顔や体のムダな動きは無いため、ハンドリング速度=検査速度となり、検査スピードは自然と上がっていくのです。
作業姿勢は、体の疲れだけではなく、検査精度にも影響を与える大事な視点であると覚えておきましょう。これが作業姿勢の視点からムダを見つけるフレームワークとなります。
3M(ダラリ)から
それでは次に、3M(ダラリ)からムダに気付くフレームワークを確認していきましょう。
「ムダ」「ムラ」「ムリ」略してダラリ
3M(ダラリ)とは、「ムダ」「ムラ」「ムリ」の頭文字Mを取って3Mと呼ばれるものです。カタカナの後ろの文字を取って、「ダラリ」とも呼びます。
このフレームワークのポイントは、ムラやムリからムダに繋がることがないかを検討することにあります。
ムラとは、「Man:技能のバラツキ」「Material:材料のバラツキ」「Machine:設備のバラツキ」「Method:手順のバラツキ」「Environment:仕事量のバラツキ」等が挙げられます。
ムリとは、「早過ぎる」「重過ぎる」「難し過ぎる」「遠過ぎる」「多過ぎる」「高過ぎる」「低過ぎる」「熱過ぎる」といったような、何々過ぎると言ったものが挙げられます。
こんなダラリは起きていない?
例えば、あなたの現場では、こんなことは起きていないでしょうか。
1日の時間帯あるいは1ケ月の中で、ムリをしなければ仕事がこなせなくなり、仕事の質よりもこなすことが優先されてしまったり、かと思えば、手待ちになるタイミングが発生してしまったりというケースです。
このようなケースでは、1日や1ケ月の中でムリやムラが発生していることになります。これらを改善することで、生産性の向上に結び付いていくのです。
これが3M(ダラリ)からムダを見つけるフレームワークとなります。
照度、休憩、温度等の環境から
それでは次に、照度、休憩、温度等の作業環境からムダに気付くフレームワークを確認していきましょう。
作業環境の悪さはヒューマンエラーの誘発や作業効率の低下に繋がる
照度、休憩、温度等の作業環境が悪いとどうなるでしょうか。
照度が適正でないと、正確さが落ち、作業効率が低下してしまいます。
必要な休憩を取っていなかったり、作業場所の温度が暑かったり寒かったりすると、集中力の低下によるヒューマンエラーの誘発や作業効率の低下に繋がってしまいます。
適正な照度環境を整え安全かつ快適に作業を
照度に関しては、適正な照度環境を整えることで、安全かつ快適に作業を行なえる状態を構築していくようにしましょう。
一般に、照度は、lx(ルクス)という単位を使います。
事業者は、一定期間ごとに測定を行ない、作業環境が適切に維持されているか確認することが求められていることも覚えておきましょう。
労働安全衛生規則においても、ここに示すような基準が設定されています。
明るすぎても暗すぎてもいけない
照度は、明るすぎても暗すぎてもいけません。照度の推奨値はココに示す通りです。
ごく粗い視作業では70~100lx、荷物の積み降ろしでは100~150lx、組立や検査、試験をともなわない作業では150~300lx、一般の製造工程における視作業では300~750lx、選別、検査、分析など細かい視作業では750~1500lx、精密機械、電子部品の製造、印刷工場での極めて細かい視作業では1500~3000lxが一般的な基準です。
もちろん作業の特性によっても異なりますので、必ずしもこれが当てはまらないケースもあるかもしれません。
大事なことは、「この作業場で適した照度はどのくらいか明確にする」ことです。その基準に対して定期的に守られているかチェックを行なっていくことが求められているのです。
工場では作業しやすい明るさを保つための工夫が必要
明るさを適切に保ち、快適に作業をするためにはどのような対策が必要なのでしょうか。
工場では作業しやすい明るさを保つために、さまざまな工夫が必要です。実際に工場で行われている対策を3つ紹介します。
1つ目は、LED照明です。
明るくしたい箇所に集中して光を当てることができるため、細かい作業をする場所に適しています。光にちらつきがないため目の負担が少なく、検査や選別等がしやすくなるのです。結果的に作業の効率が上がり、蛍光灯よりも寿命が長くコスト低減にもつながります。
2つ目は、スポット照明です。
精密機械等の細かい作業においては、手元に光を当てるためのスポット照明を取り付けることも有効です。また、製品の最終チェックをするといった集中力のいる入念な作業でも、スポット照明が活用されます。
3つ目は、本体やカバーの清掃です。
照明器具に汚れがつくと、大きく照度が落ちてしまいます。カバー等の汚れやすい箇所は、定期的に清掃しきれいにすることが大切です。照明器具の汚れもムダの1種ということですね。
作業の正確さと効率を上げるためには、明るさが重要です。明るさは現場で働く人がムダなく安全に作業できるように、とても重要なことなのです。普段現場を巡回する際には、「本当にこの明るさで大丈夫か」と疑問を持つことが大切です。
照度測定器や照度の測定できる無料アプリ等も活用し、早速照度を測定してみましょう。
休憩や湿度にも考慮が必要
休憩の確保に関しては、労働基準法に則り、6時間超8時間以内の場合には45分、8時間を超える場合には1時間の昼休憩を確実に取るようにしましょう。そして、1.5~2時間に1度は10分程度の小休憩を取り、高温の日には、いつもより多く長く休憩を取る等の配慮をすることも欠かせません。
また、作業場の温度・湿度によっても、生産性が大きく変わります。業種や仕事の内容によって異なりますが、基準として20~25度が最適と言われています。
更に、湿度は温度に対する感じ方に影響を及ぼすため、温度だけでなく湿度も重要です。湿度が低すぎると、作業効率悪化や健康被害が生じてしまうので注意するようにしてください。
以上で挙げたような作業環境は、基準から外れている場合、直接的・間接的にムダに繋がります。目に見える動作のムダだけではなく、これらの環境面でのムダもおろそかにせず、ムダ取り活動を行なっていきましょう。


ムダ取りフレームワークを使ったムダ発想法のまとめ
以上で学んだことをまとめてみましょう。
ムダとは?ムダ発想法とは?
- ムダとは、“付加価値”を付けていること以外の全てのこと
- 顧客視点のムダとは、自分達にとって必要のない「明らかなムダ」だけではなく、顧客にとって価値のある付加価値作業に当てはまらないムダのこと
- ムダを取ると、労務費・材料費・経費が減ることで、利益へ繋がる
- ムダは先入観や無知から生まれる。先入観による思い込みや知らないがためにムダは生まれることが多い
- 現場においては、作業のムダが不満となって現れることが多い。従って、不満を解消してあげることはムダを取ることに繋がる
- 作業姿勢が適正でないと、集中力の低下、モチベーションの低下、作業時間のバラツキ発生に繋がってしまう
- 3M(ダラリ)とは、ムダ、ムラ、ムリのこと。ムラ、ムリはムダに繋がるため、ムダ取り活動の対象になる
- 照度を適正にすると、疲れや見落としを低減することになり、ムダ取りに繋がる
- 作業環境における改善もおろそかにせずにムダ取り活動を進めていくことが大切
いかがでしたか?ムダ取りの視点はイメージできましたか?
様々なムダを見つけるフレームワークを覚えておき、現場でいろいろな視点からムダを見つけていきたいですね!


関連学習動画
-
k2-19
アニメで学ぶIE実践編~応用手法 Part2~
有料サービス限定
Lesson5:レイアウト改善の6つの視点 前編
受講対象者
全部門(管理職)- カリキュラム構成
-
- はじめに
- レイアウト改善の狙い
- レイアウト改善の6つの視点①
- レイアウト改善の6つの視点②
- レイアウト改善の6つの視点③
- まとめ
-
k2-11
アニメで学ぶ“IE実践編~動作研究 Part2~”
有料サービス限定
Lesson6:サーブリッグ分析とは 後編
受講対象者
係長向け,次長・課長向け- カリキュラム構成
-
- サーブリック記号の3分類 Ⅱ類
- サーブリック記号の3分類 Ⅲ類
-
k2-16
アニメで学ぶIE実践編~運搬分析 Part1~
有料サービス限定
Lesson3:運搬の基本原則 後編
受講対象者
全部門(管理職)- カリキュラム構成
-
- はじめに
- 手持ちや空運搬に関する原則
- 能力向上や作業改善に関する原則
- 移動経路に関する原則
- まとめ
-
k2-01
アニメで学ぶ”トヨタ生産方式~入門編~”
有料サービス限定
4:ジャストインタイムの3原則と後工程引き取り
受講対象者
現場部門, 間接部門, 一般, 主任・班長クラス, 係長クラス, 課長クラス- カリキュラム構成
-
- ジャストインタイムの3原則とは
- 後工程引き取りとは
- 後工程引き取りとカンバンの関係
- カンバンの注意点
- まとめ
-
k2-17
アニメで学ぶIE実践編~運搬分析 Part2~
無料会員限定
Lesson2:運搬活性分析図を使った改善事例
受講対象者
全部門(管理職)- カリキュラム構成
-
- はじめに
- 事例(改善前)
- 事例(改善後)
- まとめ
-
k2-15
アニメで学ぶIE実践編~稼働分析 Part2~
無料会員限定
Lesson2:ワークサンプリング“事前準備フェーズ”
受講対象者
係長向け,次長・課長向け- カリキュラム構成
-
- ワークサンプリングの実施方法
- ①~④のポイント
- ⑤、⑥のポイント
- まとめ