後工程引取り生産とは?過剰在庫のムダは新たなムダを生む
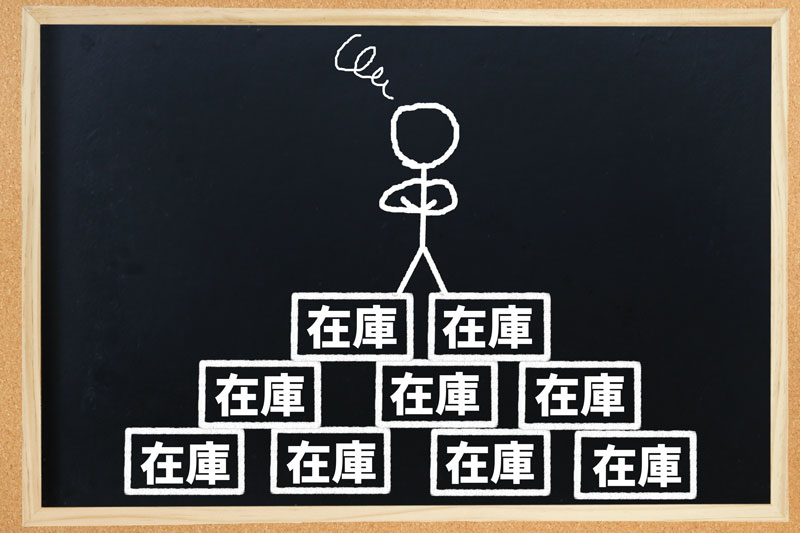


後工程引取りとは
造る側の都合を排除し、お客様への販売を起点にする後工程引取り
後工程引取りとは、後工程が、「必要なモノを、必要な時に、必要な分だけ」、前工程から引き取る方法のことです。ジャストインタイムの3原則の1つです。
後工程引取りの流れを繋げ、お客様のニーズに沿った生産をするために、かんばんをツールとして活用します。後工程引取りは、「造る側の都合を排除し、お客様への販売を起点にする」ことがポイントです。あくまで起点は、お客様への販売になります。
ジャストインタイムの3原則については下記のページで詳細を解説しています
[reg-bnr] 本ページでは、トヨタ生産方式の2本柱である「ジャストインタイム」について、前提条件や「後工程引取り」「工程の流れ化」「必要数でタクトを決める」の3原則、成功ポイントについて解説しています。 ジャストインタイムとは...
過剰在庫は2次的なムダを生む
後工程引取りは、在庫を最小化するための手段でもあります。その意味を確認していきます。
ある工場に、過剰在庫があると仮定しましょう。
ムダ排除の考え方がしっかりと徹底されておらず、過剰在庫を「過剰」と認識できない場合、どのように2次的なムダが発生していくか、確認していきます。まずはじめに、在庫が工場内に入りきらないと、倉庫が必要だと考え、大きな投資をしてしまいます。
これはもちろん、原価アップに繋がります。そして、倉庫を建てると、今度はリフトの購入と運搬作業者の設置が必要になります。
リフト購入による原価アップはもちろん、運搬作業者は新たに採用すると、当然労務費もアップします。そして、在庫が増えてくると、今度は防錆処理や在庫管理のために、人員が必要になります。これも労務費アップです。
そして、部品や材料が倉庫に滞留する時間が長くなってくると、出庫時に手直しが必要になってきます。手直しの数が増えてくると、また増員しなければいけなくなります。そして、そのうちに在庫の数も倉庫の大きさの分だけ大幅に増え、在庫管理が大変になってくると、在庫管理のシステムが必要になります。在庫管理のシステムも大きな投資であり、それを取り扱う人員もまた必要になります。
そして、その在庫管理が適切に行われていないと、現場では欠品が発生します。そうすると、生産能力が足りないことが原因だと考え、設備増設を考えるようになります。これも原価を上げる要因になります。最終的には、更に在庫が増えていく悪循環に陥っていきます。
ムダがムダを生むという意味
過剰な在庫は、新たなムダを生みます。そしてそのムダが、新たなムダを生んでいきます。
- 過剰な倉庫新設への投資金額
- 過剰な在庫運搬作業者の採用とリフトの購入金額
- 過剰な在庫管理の人員採用
- 過剰な手直し作業者の人員採用
- 過剰な在庫管理システムへの投資金額
- 過剰能力のための設備投資金額
これらは全て過剰な投資、つまりムダであり、原価を上げることになります。このように、過剰在庫のムダにより、2次的なムダを生むという悪循環が発生するのです。
今回の例は最悪の事態を想定していることで、少々極端な例ですが、程度の差こそあれ、似たようなことは十分に起こる可能性があります。経営者はもちろん、現場管理者は、何がムダを生むのか、ムダを生まないためにはどんな考え方をすべきなのか、今一度ムダに関する考え方をしっかりと認識するようにしましょう。
たかが在庫といっても、数パーセントしかない利益を食い尽くしてしまう可能性があります。決して甘く見ないようにしてください。


後工程引取り生産の成功条件とは
定量不定時運搬と定時不定量運搬の違い
運搬は、基本的に2つの方法で行ないます。
定量不定時運搬
1つは、定量不定時、もう1つは定時不定量での運搬です。定量不定時運搬とは、毎回一定に決まった量を不定期に運搬する方法です。例えば、毎回100個の部品という決まった量を、指示を受けた都度運ぶという形を取ります。部品が必要なタイミングは、かんばんが外れるタイミングにより判断を行ないます。
定時不定量運搬
一方で、定時不定量運搬とは、毎回決まった時間に必要な量を運搬する方法です。例えば、2時間置きに、指示を受けた必要数量の部品を運ぶという形を取ります。必要数量はかんばんの枚数によって判断されます。
定量不定時運搬と定時不定量運搬、どちらを選ぶ?
定量不定時運搬と定時不定量運搬、どちらを選んだらよいのでしょうか?
工場内は原則定量不定時運搬
工場内は、原則、定量不定時運搬を選択します。後工程の部品の使用が一定量に達したら、かんばんが発行され、引き取りにいきます。
前工程が遠隔地の場合は原則定時不定量運搬
一方で、サプライヤー等、前工程が遠隔地の場合は、原則、定時不定量運搬を選択します。事前に定められた時間に運搬し、供給量は後工程の生産量次第となり、一定量ではありません。
以上が運搬の原則となりますが、その企業・工場の特徴や管理レベルに応じて、選択していくことになります。特に工場内に関しては、徐々に物流管理レベルを上げながら、最終的に定量不定時運搬を目指していくことが求められます。
後工程引取り生産における成功の条件
後工程引取り生産を成功させるには、どのようなことが条件になるのでしょうか?
例として、機械加工された部品が、後工程の組立工程に供給される製品を想定して説明します。この製品の生産予定数が、このように毎日一定数で予定されていると仮定します。
後工程の組立工程は、生産予定線に沿って、淡々と進捗していることが理想です。この場合、前工程の機械加工工程も予定数を確実にこなしてさえいれば、後工程引取りを行なっても全く問題は発生しません。
後工程が遅れと挽回を繰り返した場合
一方で、後工程である組立工程が、このように遅れと挽回を繰り返す生産を行なってしまった場合はどうなるでしょうか。
後工程引取り生産を行なう場合、後工程が今必要としていないモノは造ってはいけません。
よって、前工程の在庫置き場がある一定量溜まったら、生産をストップしなければいけません。図中の矢印の部分がそのタイミングになります。
このケースでの問題点は、次のどれにあるのでしょうか。
① 後工程引取りがこの工場にマッチしていないこと
② 前工程が後工程の変化に付いていける能力を持っていないこと
③ 後工程である組立工程の生産数の振れが大きいこと
実は、後工程引取り生産にトライし、途中で諦めてしまった企業では、①と②が原因だと決めつけてしまい、可能性を潰してしまっているケースが多々存在します。本当は後工程引取り生産が可能なのに、すぐに可能性を潰してしまうのは、非常に勿体ないことです。
後工程の平準化レベルを上げていくことがポイント
もうお分かりのように、③の後工程である組立工程の生産の振れが大きいことを解決しなければ、後工程引取り生産は成立しません。つまり、後工程の平準化レベルを上げていくことがポイントです。逆に言うと、後工程引取り生産のレベルを地道に上げていけば、製品の生産の流れの全体において、どこに異常があるかすぐに発見できます。
その発見できた異常を 地道に対策していくと、ムダがどんどん削減され、コストが低減していきます。このことが理解できるかが、トヨタ生産方式の導入が成功できるか、分かれ道になっていると言っても過言ではありません。
地道な取り組みを大きな成果へ
平準化された計画を毎日確実にこなしていくこと
やはり、目指す姿は、一定の生産を淡々と進捗している状態です。後工程引取り生産を成立させるために、平準化された計画を毎日確実にこなしていくことが必要不可欠です。
地道な取り組みは、将来の大きな成果に必ず繋がる
そして、毎日確実に生産計画を達成していくためには、標準作業、平準化、かんばんの運用、そして5S等、地道な取り組みの徹底が必要不可欠です。現在行っている地道な取り組みは、将来の大きな成果に必ず繋がります。
熱意とチームワークで諦めずに!
そして、もうひとつ。熱意とチームワークで諦めずに目指したい姿へ向かって進んでいくことが大切です。


後工程引取り生産のまとめ
以上で学んだことをまとめてみましょう。
後工程引取り生産とは?過剰在庫のムダは新たなムダを生む
- 過剰在庫になると、“追加”の倉庫新設、“追加”のリフトや運搬作業者、“追加”の倉庫の管理者、“追加”の手直し担当者、“追加”の在庫を管理するシステム、“追加”の生産設備等が発生する
- たかが在庫という考えでは、2次的なムダが誘発されてしまうため、「在庫はムダを生む」ということをしっかりと頭に入れておかなければいけない
- 2次的なムダは、新たなムダを呼び、数パーセントしかない利益を食い尽くしてしまうことにもなりかねない
- 決して在庫を甘く見ずに、日々在庫を抑え、コントロールしていくことが必要不可欠
後工程引取り生産の成功のために
- 運搬の基本的な2つの方法は「定量不定時運搬」と「定時不定量運搬」
- 工場内は基本的に定量不定時運搬、遠隔地のサプライヤー等は定時不定量運搬で考えるのが基本
- 後工程引取り生産がうまくいかない一番の原因は、後工程(特に最終工程)の生産数の振れが大きいこと
- 後工程が平準化できていなければ、前工程は変動に追従しなければいけなくなり、この変動は上流工程に遡っていく程大きくなり、大き過ぎると追従しきれなくなってしまう
- 後工程引取り生産を成立させるためには、後工程を平準化させた計画を立てる力と、計画を淡々とこなしていけるような製造力が求められる
いかがでしたか?後工程引取り生産の概要はイメージできましたか?在庫は、そのものだけではなく、新たなムダを生むリスクを持っています。最適在庫が常に維持されるような仕組みづくりを目指していきたいですね!


関連学習動画
-
k2-01
アニメで学ぶ”トヨタ生産方式~入門編~”
有料サービス限定
9:ニンベンの付いた自働化の狙い
受講対象者
現場部門, 間接部門, 一般, 主任・班長クラス, 係長クラス, 課長クラス- カリキュラム構成
-
- トヨタ生産方式の2本柱
- ニンベンが付いた「自働化」とは
- 「自働化」で置き換える3つの人の働き
- ニンベンの付いた「自働化」の目的
- ジャストインタイムとの関係
-
k2-01
アニメで学ぶ”トヨタ生産方式~入門編~”
無料会員限定
2:トヨタ生産方式の基本思想と2本柱
受講対象者
現場部門, 間接部門, 一般, 主任・班長クラス, 係長クラス, 課長クラス- カリキュラム構成
-
- トヨタ生産方式の基本思想とは
- トヨタ生産方式の2本柱とは
- ジャストインタイムとは
- ニンベンの付いた自働化とは
- まとめ
-
k2-01
アニメで学ぶ”トヨタ生産方式~入門編~”
有料サービス限定
4:ジャストインタイムの3原則と後工程引き取り
受講対象者
現場部門, 間接部門, 一般, 主任・班長クラス, 係長クラス, 課長クラス- カリキュラム構成
-
- ジャストインタイムの3原則とは
- 後工程引き取りとは
- 後工程引き取りとカンバンの関係
- カンバンの注意点
- まとめ
-
k2-02
アニメで学ぶ”トヨタ生産方式~初級編~”
有料サービス限定
5:省人化、少人化の違い
受講対象者
生産部門全般 一般- カリキュラム構成
-
- 省力化、省人化の違い
- ジャストインタイムと少人化
- 少人化ラインをつくるには
- まとめ
-
k2-02
アニメで学ぶ”トヨタ生産方式~初級編~”
有料サービス限定
3:人の“働き”と“動き”の違い
受講対象者
生産部門全般 一般- カリキュラム構成
-
- 「働き」と「動き」の違い
- 「動き」を「働き」に変えていく
- 付加価値を付けるとは
- 付加価値かどうかの判断方法
- まとめ
-
k2-01
アニメで学ぶ”トヨタ生産方式~入門編~”
有料サービス限定
6:ボトルネック・ラインバランス・同期化
受講対象者
現場部門, 間接部門, 一般, 主任・班長クラス, 係長クラス, 課長クラス- カリキュラム構成
-
- ボトルネック工程とは
- ラインバランス改善とは
- 同期化とは
- まとめ