現場で大事な2つの指標とは?人時生産性と設備稼働率の意味と計算方法を解説
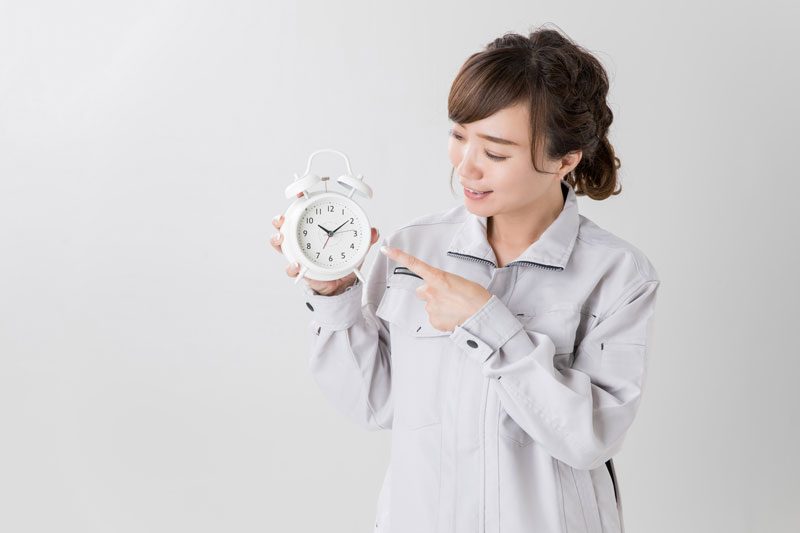


現場で大事な2つの指標とは
生産現場では、様々な指標が管理されています。その中でも特に重要な2つの指標は何かわかりますか?人と機械でそれぞれ1つ挙げてみましょう。
そう、正解は「人時生産性」と「設備稼働率」ですね!
生産現場では、人と設備のそれぞれ、2つの指標を適切な考え方で運用していくことが大切です。本ぺージでは、人時生産性とは何か?設備稼働率とは何か?概要や考え方、ポイントについて解説を行います。


人時生産性とは
人時生産性の考え方
それではまずは、人の効率に関わる指標である、人時生産性について確認していきましょう。
人の効率を管理する大事な指標!
まずは、「人時生産性の考え方」について確認します。
生産現場で人の効率を管理する大事な指標である「人時生産性は」1人、1時間あたりの生産性を表します。「じんじ」ではなく、「にんじ」と読みます。
労働量に対して、どれくらいの生産が得られたか
この人時生産性は、投入した労働量(INPUT)に対して、どれくらいの生産(OUTPUT)が得られたかを表す指標です。
人時生産性は、このように、アウトプット割るインプットで計算します。
生産現場における人時生産性
生産現場における人時生産性をもう少し具体的に表すと、一定期間における生産金額あるいは生産量、出来高工数等を、一定期間における総労働時間で割ることで求めます。
人時生産性の指標を活用する狙いは、「少ない作業時間で沢山の製品を造れるようになった時に、その頑張りがどのくらいか、客観的に分かるようにする」ためです。
作業のスピードアップの場合
では、簡単な事例をもとに、人時生産性の変化を確認します。
まずは、作業のスピードアップによる、人時生産性の向上です。
例えば、改善前は、6人1時間で60,000円の製品を造ったとします。この時の人時生産性は、60,000円を6人かける1時間で割り、10,000円です。
では、改善により2倍にスピードが向上した時は、人時生産性はどう変化するでしょうか。同じように計算すると、60,000円を6人0.5時間で割り、人時生産性は、20,000円となります。
つまり、半分の時間で作業が完了すると、生産性は2倍となるのです。
省人化の場合
次に、作業自体をなくし省人化した際の人時生産性の向上について確認します。
先ほどと同様に、改善前の人時生産性が10,000円の時、2名分の作業を機械化したとします。人時生産性を計算すると、60,000円を4人1時間で割り、15,000円となります。
つまり、機械化により、6人が4人になり、人時生産性は1.5倍に向上するのです。簡単ですよね!人時生産性の計算は、このような考え方が基本となります。
人時生産性が向上する主なパターン
では、人時生産性が向上する主なパターンを押さえておきましょう。
1つ目は、生産量が増加し、作業時間が減少するパターンです。これは生産量が増えたのに、作業の時間は少なくなるので、人時生産性が向上するのはすぐに分かりますね!
2つ目は、生産量が増加し、作業時間が横ばいのパターンです。これも生産量は増えているのに、同じ時間で作業が出来たことになるので、人時生産性が向上するのは当然ですね。
3つ目は、生産量が横ばいで、作業時間が減少するパターンです。生産量が増えなくても、作業時間が減っているので、人時生産性は向上するのは分かりますね。
4つ目は、生産量が減少してしまうものの、それを上回るくらい作業時間が減少するパターンです。生産量が減少しているのであれば、作業時間を大幅に減らすアプローチが必要ということですね。
5つ目は、作業時間が増加してしまうものの、それを上回るくらい生産量を大きく伸ばすパターンです。作業時間が増加した分以上に生産をすることができれば、人時生産性という視点から見ると改善していることになります。
これら5つのパターンが基本形です。販売動向等から自職場の置かれた状況を考え、どのパターンで人時生産性を向上させるか、イメージしながら改善を進めていくようにしましょう。
実務における人時生産性の運用について
出来高工数を生産投入工数で割る
では次に、「実務における人時生産性の運用について」確認していきます。
就業時間を基準に考えていきます。就業時間とは会社にいる時間のことで、対象となる全人員に対して、タイムカード等で管理された時間を合計したものです。
一般に、就業時間の中には、作業を行なっているだけではなく、他部門応援をしていたり、改善活動を行なった時間があるはずです。
A:生産投入工数は、就業時間からこれらの除外工数を引いたものになります。
さらに、A:生産投入工数の中には、直接的に作業を行なっていた時間のほかに、間接業務や手待ち等の時間があるはずです。
B:直接工数は、A:生産投入工数から、これらの時間を引いたものになります。
そして、B:直接工数の中には、良品を作っていた時間のほかに、作業ロスや不良ロスによって、お客様に販売できる状態の製品を造っていない時間が出てきます。
C:出来高工数は、B:直接工数からこれらの時間を引いたものになります。
以上を踏まえ、生産現場では、人時生産性をこのように、C:出来高工数をA:生産投入工数で割る形で管理します。
意味合いとしては、出来高工数は、「生産に掛けるべき時間」、生産投入工数は、「実際に掛けた時間」となります。
人時生産性は作業能率と生産効率の2つに分解して扱う
さて、実務におけるポイントを確認しましょう。
生産現場における運用においては、人時生産性をこのように2つに分解して管理します。
1つは、C:出来高工数をB:直接工数で割ったもので、作業能率です。
もう1つは、B:直接工数をA:生産投入工数で割ったもので、生産効率となります。
それぞれの持つ意味を確認しましょう。
作業能率
作業能率は、持ち場にいる時間の中で、「どのくらい製品をつくることが出来たか」を表します。
生産効率
生産効率は、会社にいる時間の中で、「持ち場でモノを造る作業を行なうことが出来ていた時間の割合」を表します。
人時生産性(作業能率×生産効率)運用のポイント
運用のポイントは、次のこととなります。
まず、能率×効率が生産性であること。そして、能率が上がっていても、効率が落ちていたら生産性は上がらないこと。
効率が上がっていても、能率が落ちていたら生産性は上がらないこと。
つまり、能率と効率の両方を管理していく必要があることをしっかりと覚えておきましょう。
ケーススタディ
作業能率はどんなことで下がる?
それでは、能率、効率をケーススタディで確認していきます。まず、作業能率は、どんなことで下がり、何をすれば上げることができるでしょうか。
まずは、どんなことで能率は下がるか、いくつか低下要因を挙げてみましょう。
・習熟度が低い人がラインに入り数が落ちる
・標準作業がつくり込まれておらず、バランスが悪い
・トラブルが発生し、度々流れが止まってしまう
・時間を意識せずに何となく作業をしている
・ムリな作業設計になっている
それでは、これらの低下要因は、何をすれば上げることが出来るか、いくつか対策例を挙げます。
・作業の習熟度を向上させる
・ムダを排除した標準作業の作り込みを行なう
・トラブル原因を日々潰し込む
・時間を意識できる仕組みを導入し、目標管理する
・ムリな作業を撲滅し、リズミカルな作業にする
これらのことを行なうことで、能率は向上させることが可能となります。能率改善の際のテーマの参考にしてみましょう。
生産効率はどんなことで下がる?
同様に、生産効率は、どんなことで下がり、何をすれば上げることができるのか、考えてみましょう。
まず、効率の低下要因としては、どんなことが思い浮かびますか?いくつか低下要因を挙げてみましょう。
・材料待ちが発生する
・指示待ちが発生する
・トラブルでライン・設備が停止する
・必要以上の間接仕事がある
・突発休暇等の人員調整に追われる
・段取・切替が長く掛かる
・3S時間が長く掛かる
それでは、これらの低下要因は、何をすれば挙げることが出来るか、考えて見ましょう。では、いくつか対策例を挙げます。
・JITで材料を供給する
・事前に準備するやり方へ変える
・トラブルを日々潰し込む活動を継続する
・間接仕事のムダを排除する
・残業・休暇等の人員管理を適正化する
・段取・切替時間短縮を推進する
・乱れない・汚れない仕組みをつくる
これらのことを行なうことで、効率は向上させることが可能となります。効率改善の際のテーマの参考にしてみましょう。
○×問題で試してみよう!
それでは次に、○×問題を出しますので、答えてみましょう。
第1問
1日8時間稼動で120個生産していたのを、2時間残業し150個生産しました。
この時、人時生産性は上がるでしょうか?下がるでしょうか?変わらないでしょうか?
正解は、×です!このケースでは、時間当たりの生産は15個なのは一緒なので、生産性は変わりませんね!
第2問
従来1日4人体制で100個生産していたのを、1日6人体制で150個生産しました。
この時、人時生産性は上がるでしょうか?下がるでしょうか?変わらないでしょうか?
正解は、×です!このケースでは、1人当たりの生産は25個なのは一緒なので、生産性は変わりませんね!
第3問
従来1日4人体制で100個生産していたのを、1日4人体制で120個生産しました。
この時、人時生産性は上がるでしょうか?下がるでしょうか?変わらないでしょうか?
正解は、○です!このケースでは、1人当たりの生産は25個から30個に増えたので、生産性は上がりますよね!
第4問
従来1日8人体制で100個生産していたのを、1日6人体制で100個生産しました。
この時、人時生産性は上がるでしょうか?下がるでしょうか?変わらないでしょうか?
正解は、○です!このケースでは、1人当たりの生産は12.5個から16.7個に増えたので、生産性は向上しますよね!
第5問
加工治具の改造で、平均不良率が8%から4%に低減しました。この時、人時生産性は上がるでしょうか?下がるでしょうか?変わらないでしょうか?
正解は、○です!このケースでは、不良率の低減により、ムダな生産がなくなるので、当然生産性は向上します。
第6問
8時間掛かる作業を7時間で終了させ、残り1時間で清掃作業を行ないました。この時、人時生産性は上がるでしょうか?下がるでしょうか?変わらないでしょうか?
正解は、×です!このケースでは、作業時間は改善されているものの、ただ清掃に余力時間を当てただけなので、生産性は変わりません。
第7問
8時間掛かる作業を7時間で終了させ、残り1時間で改善活動を行ないました。この時、人時生産性は上がるでしょうか?下がるでしょうか?変わらないでしょうか?
正解は、△です!このケースでは、余力時間で改善活動を行なっても、その日の生産性は変わりません。ただし、改善活動は将来の生産性向上に繋がる、という視点で△となります。
第8問
8人作業を7人作業に改善し、1名を事務作業に回しました。この時、人時生産性は上がるでしょうか?下がるでしょうか?変わらないでしょうか?
正解は、×です!創出した余力時間を間接作業に回しても、生産性は向上しません。能率は上がっても効率が下がってしまい、結果的に生産性が変わらないケースです。
いかがですか?生産性向上のイメージは付いたでしょうか?よくありがちなことは、生産を増やせば生産性が上がると思い込んでいるケースです。いくら生産が増えても、時間当たりの出来高が増えない限りは生産性は向上しません。
また、改善により余力が出ても、それを生産性向上まで結びつけることが出来ていないケースも見受けられます。どのようなことを行なえば生産性が向上するのかを、しっかりとイメージして改善を進めていくようにしましょう。


設備稼働率とは
それでは次に、機械の効率に関わる指標である、設備稼働率について確認していきましょう。
設備稼働率とは、一定の期間において、設備・機械がどのくらいの割合で動いていたかを表す指標です。
設備の効率を阻害する7大ロスとは
3つのロスの視点
まずは、「設備の効率を阻害する7大ロス」について確認していきましょう。設備の稼働に関する時間とロスの関係をイメージ図で確認します。
まず第一に工場は、操業時間が決まっています。
この操業時間の中には、実際に設備に電源を入れて負荷を掛けている「負荷時間」があります。
一方、生産量が少ない場合は、無理に設備を動かす必要はないため、計画停止を入れることも出てきます。
そして、負荷時間の内訳を見ると、実際に設備が稼働していた「稼働時間」と、設備が停止していた「停止ロス時間」に分けられます。
更に、稼働時間の内訳も見てみると、設備本来の性能を発揮できていた「正味稼働時間」と、性能が落ちてしまっていた「性能ロス時間」に分けられます。
正味稼働時間も更に細分化すると、しっかりと良品を造っていた「価値稼働時間」と、不良を造ってしまっていた「不良ロス時間」に分けることが出来ます。
このように、負荷時間の中には、大きく3つのロスがあり、これらが設備の効率を低下させてしまい、経過時間あたりの良品出来高を下げてしまうのです。
停止ロス
では、それぞれのロスの詳細を確認してみます。
停止ロスには、大きく次の4つが挙げられます。故障ロス、切替え調整ロス、治具交換ロス、立上りロスです。
その他にも、清掃点検、指示待ち、材料待ち、配員待ち、品質確認待ち、測定調整等があります。
品種切り替え、段取り替え、ドカ停、昇温待ち等がこれらの4つの停止ロスに当てはまりますね!
性能ロス・不良ロス
性能ロスに関しては、チョコ停空転ロス、速度低下ロスが挙げられます。チョコ停とは、数秒・数分程度の小さなトラブルが多発することを指します。
速度低下ロスは、機械の劣化によるスピード低下などが当てはまりますね!
不良ロスに関しては、不良手直しロスが挙げられます。不良だけではなく、手直しをすることにより生じたロス時間もここに含まれます。
ここまでに挙げた7個のロスが、設備の7大ロスと呼ばれるものになります。
実務においても、この7つに関しては日報集計が必要となりますので、確実に覚えておくようにしましょう。
設備稼働率の考え方~時間稼働率~
では次に、設備稼働率の考え方について確認します。先ほどのイメージ図をもとに、いくつかの設備の管理指標を押さえておきましょう。
1つ目は、時間稼働率です。稼働時間を負荷時間で割ったもので表します。
時間稼働率は、設備に電源が入っていた時間の中で、トラブル等が無く稼働していた時間の割合を意味しています。
停止ロスが大きくなるほど、この指標は低下してしまうため、いかに停止を起こさないかが大切となります。
設備稼働率の考え方~性能稼働率~
2つ目は、性能稼働率です。正味稼働時間を稼働時間で割ったもので表します。
性能稼働率は、設備が動いていた時間の中で、設備が持つ性能通りに稼働していた割合を意味しています。性能ロスが大きくなるほど低下してしまう指標となり、いかに設備の持つ本来の性能を発揮できるように設備を維持管理していくかが大切になります。
設備稼働率の考え方~良品率~
3つ目は、良品率です。価値稼働時間を正味稼働時間で割ったもので表します。
良品率はその名の通り、不良を造ってしまうほど、低下してしまう指標です。いかに良品を造り続けることができるかが大切となります。
設備稼働率の考え方~設備総合効率~
そして、以上3つの指標、時間稼働率、性能稼働率、良品率を総合したものとして、設備総合効率という指標があります。
価値稼働時間を負荷時間で割ったもの、あるいは、3つの指標を掛け合わせたもので表します。最終的な価値稼働時間を増やすために、停止ロス、性能ロス、不良ロスを総合的にどのくらい低減することができたかを客観的に判断することができます。設備の管理レベルは、最終的にはこの設備総合効率をいかに向上させられたかで評価がされ、これを向上させるために、日々設備の保全を継続していくことが大切です。
日々の設備稼動率の運用
運用のポイント
日々の設備指標の管理は、こちらの参考例で示すように、日々各指標がどのような変化をしているか、モニタリングをしていくことで行ないます。
このように各指標の推移が見える化されると、例えば、特定の日にちで時間稼働率が大きく低下していることが読み取れます。この日の特徴を調べてみると、切り替え段取り実施日に指標は低下していることが判断でき、この職場では、切替時間短縮をテーマに活動していくことにより、設備総合効率を大きく上昇させられることが特定できます。
このように、指標を管理することではじめて、自職場の課題を明確にすることができます。日々しっかりと指標管理を行なっていくことが、稼動率改善の入り口となるのです。
ケーススタディ
それではケーススタディで考え方を確認してみましょう!
これからいくつか問題を出します。それぞれのケースでは、時間稼働率、性能稼働率、良品率のうちどの指標が低下するでしょうか?
第1問
加工中に不良が出てしまうので、スピードを落として動かした。
このケースでは、どの指標が低下するでしょうか?
正解は、性能稼働率です。
このケースでは、スピードを落としてしまう、つまり性能を落としてしまうことになります。従って、性能ロスが発生することになり、性能稼働率が低下してしまうのです。
第2問
いつもより切替時間が余計に掛かってしまった。
このケースでは、どの指標が低下するでしょうか?
解は、時間稼働率です。このケースでは、切替時間が余計に掛かる、つまり機械の停止時間が長くなってしまうことになります。従って、停止ロスが発生することになり、時間稼働率が低下してしまうのです。
第3問
第3問、加工したモノがいつもより多く不良ではじかれた。
このケースでは、どの指標が低下するでしょうか?
正解は、良品率です。このケースでは、不良がいつもより多く発生しているということですので、不良ロスが増加してしまうことになります。従って、良品率が低下してしまうのです。
第4問
第4問、加工中にチョコ停が頻発し、必要数に達しなかった。
このケースでは、どの指標が低下するでしょうか?
正解は、性能稼働率です。このケースでは、チョコ停が頻発しているということですので、設備が本来の能力を発揮していないということになります。従って、性能ロスが発生し、性能稼働率が低下してしまうのです。なお、間違いやすいものとして、長時間停止(ドカ停)とチョコ停があります。この2つを混同し、停止ロスと性能ロスのどちらに入れるのかを迷ってしまうことがあります。
覚え方として、長時間停止は、「停止時間を記録できるほど長く停止したもの」、チョコ停は、「数秒から数分程度の短い時間での停止であり、実務上は全ての時間を記録できないもの」と区分するとよいでしょう。
練習問題(計算練習)
では次に、練習問題を行ないましょう!
次の条件における、各種設備指標を計算してみましょう。
1日の操業時間は8時間の会社です。
負荷は比較的多めで1時間残業で操業しています。
本日の加工機Aの設備停止は次の通りです。
設備のドカ停が75分、刃具交換が10分、設備立上げ時間が15分。
なお、チョコ停が何度かありましたが、詳細の時間は不明です。
加工数は200個、そのうち不良は5個、つまり良品は195個でした。
製品1個の基準サイクルタイムは120秒です。
この条件における、この日の加工機Aの時間稼働率、性能稼働率、良品率、設備総合効率を求めてみましょう。
Answer!!
それでは、順番に計算をしながら計算方法を確認していきます。
まず、負荷時間は、定時の8時間に残業の1時間を加え、9時間です。分に直すと、540分ですね。
次に、停止ロスですが、設備のドカ停、刃具交換、設備立上げ時間を合計すると100分になります。よって、稼働時間は、負荷時間の540分から停止ロスの100分を引いて、440分です。
次に、正味稼働時間ですが、加工数200個、加工サイクルタイム2分なので、400分となります。性能ロスは、稼働時間440分から正味稼働時間400分を引いて、40分です。40分に相当する時間が、本来の設備の性能を発揮出来ていなかった時間ということですね。
次に、価値稼働時間ですが、不良5個を引いた良品数195個にサイクルタイム2分を掛けて、390分です。不良ロスは、5個分になるので、10分となります。
以上の数字から、各種指標を計算してみましょう。
時間稼働率は、440/540で81.5%、
性能稼働率は、400/440で90.9%、
良品率は、390/400で97.5%、
設備総合効率は、3つを掛け合わせ、72.2%となります。
いかがでしょうか。各種指標の意味を理解して、計算式に沿って計算すれば、それほど難しくないですね。


現場で大事な2つの指標とは~人時生産性と設備稼働率~のまとめ
以上で学んだことをまとめてみましょう。
現場で大事な2つの指標とは?
- 生産現場で大事な2つの指標は、人時生産性と設備稼働率
- 人と設備、2つの指標を適切な考え方で運用していくことが大切
人時生産性とは?
- 人時生産性とは、投入した労働量(INPUT)に対して、どれくらいの生産(OUTPUT)が得られたかを表す指標
- 実務においては、人時生産性を作業能率と生産効率に分けて管理を行なう
- 作業能率は、持ち場にいる時間の中で、どのくらい製品をつくることが出来たかを表す指標
- 生産効率は、会社にいる時間の中で、持ち場でモノを造る作業を行なうことが出来ていた時間の割合を表す指標
- 片方だけではなく、両方を向上させ、全体の人時生産性を向上させていくことが大切
設備稼働率とは?
- 設備稼働率とは、一定の期間において、設備・機械がどのくらいの割合で動いていたかを表す指標
- 設備ロスの分類は、停止ロス、性能ロス、不良ロスの3つ
- 設備の効率を阻害する7大ロスは、故障ロス・切替調整ロス・治具交換ロス・立上りロス・チョコ停空転ロス・速度低下ロス・不良手直しロス
- 設備総合効率は、時間稼働率、性能稼働率、良品率を掛けたもので計算される
- 時間稼働率は、設備に電源が入っていた時間の中で、トラブル等が無く稼働していた時間の割合を表す指標
- 性能稼働率は、設備が動いていた時間の中で、設備が持つ性能通りに稼働していた割合を表す指標
いかがでしたか?本ページでは、生産現場で重要な「人時生産性」「設備稼働率」の考え方や計算方法について解説しました。実務で実際に活用していることも多い指標ですので、考え方や意味をしっかりと理解し、問題の発見や改善に繋がるように運用していきたいですね!


関連学習動画
-
k2-01
アニメで学ぶ”トヨタ生産方式~入門編~”
有料サービス限定
7:必要数でタクトを決める
受講対象者
現場部門, 間接部門, 一般, 主任・班長クラス, 係長クラス, 課長クラス- カリキュラム構成
-
- 必要数でタクトを決めるとは
- タクトタイムとサイクルタイム
- タクトタイの計算式
- ジャストインタイムの実現
- まとめ
-
k2-08
アニメで学ぶ“IE実践編~工程分析 Part1~”
有料サービス限定
Lesson4:詳細工程分析とは
受講対象者
係長向け,次長・課長向け- カリキュラム構成
-
- 詳細工程分析(フロー・プロセス・チャート)
- 工程分析記号
- 工程分析の種類と特徴
- 詳細工程分析の使い分け
- まとめ
-
k-004
【法人コース一部お試し】トヨタ生産方式基礎講座~中級編~
無料会員限定
第2章:人の「働き」と「動き」の 違い
受講対象者
生産部門全般(新入社員/一般)- カリキュラム構成
-
- はじめに
- 目次
- 働きと動きの違い
- 例題で働きと動きを判別してみよう!
- 第2章まとめ
-
k2-15
アニメで学ぶIE実践編~稼働分析 Part2~
有料サービス限定
Lesson3:ワークサンプリング“実施・分析フェーズ”
受講対象者
係長向け,次長・課長向け- カリキュラム構成
-
- ⑦のポイント
- ⑧のポイント
- ⑨の概要
- まとめ
-
i-001
【法人コース一部お試し】IE・インダストリアルエンジニアリングの概要
公開講座
第3章以降は、法人向けサービスで限定公開中!
受講対象者
生産部門、間接部門全般(中堅/管理職)- カリキュラム構成
-
IE・インダストリアルエンジニアリングの概要
第1章:IE・インダストリアルエンジニアリングとは
第2章:IEの全体像と代表的な分析手法
第3章:IEの全体像と改善活動への取り入れ方 ※法人向け限定
第4章:IE的改善へのアプローチ ※法人向け限定
-
k-018
ムダ取り入門!ムダに気付く発想法~人・方法編~
無料会員限定
2:ムダ取りフレームワーク~作業環境
受講対象者
現場部門, 間接部門, 一般, 主任・班長クラス, 係長クラス, 課長クラス- カリキュラム構成
-
- 作業環境からムダに気付くフレームワークについて
- 日頃の不満から
- 作業姿勢の視点から
- 3M(ダラリ)から
- 照度、休憩、温度等の環境から
- まとめ