構内物流とは?サービス業として現場の価値時間を向上させる構内物流
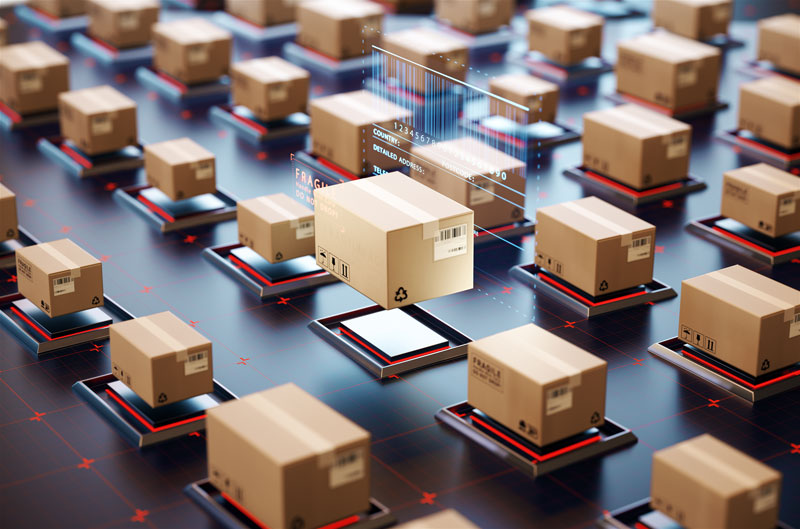


構内物流とは
本ページでは、会社全体の収益向上に貢献するために、どのような考え方、方向性で構内物流改善を進めていけばよいのかを解説します。実践で役立つ基礎知識をしっかりと学習していきましょう。
構内物流とは何か
まずは、「構内物流とは」何か、確認しましょう。
構内物流とは、工場の敷地内において、倉庫や現場間、工程間でモノを運搬することを指します。現場でモノを効率的に運ぶことは工場全体の効率化のために欠かせないため、構内物流は大事な役割の1つです。
生産工場における物流の流れは、「調達物流」として、資材・部品サプライヤーから調達を行ない、物流基地にモノが保管されます。物流基地では、モノの状態によって、荷姿変換も行なわれます。
そして、物流基地に保管されたモノは、生産管理の指示によって、生産ラインに供給・運搬されます。
生産ラインで造られた製品は、物流管理として引き取られ、物流基地に保管されます。物流基地では、モノの状態によって、荷姿変換、梱包、荷揃えが行なわれます。
最終的に、「販売物流」により得意先へ輸送されます。
この流れにおいて、この赤枠で囲った部分が、構内物流の範囲となります。
工場長になったつもりで考えてみましょう
はじめに、あなたへ質問です。工場長になったつもりで考えてみましょう。
自動車部品を製造するA社は、全社的な生産改革と一環として、構内物流改善に取り組むことに方針が決まりました。この時、物流部門が最初に取り組むべき物流改善の課題として、工場長が指示すべき項目は次の内のどれでしょうか。
- 今までやってきた物流作業を5%の人員を無条件で抜いて実施してみる。
- 一週間かけて物流工数が削減できるアイテムを発掘し、それを1つずつ潰していく。
- 物流工数には手をつけず、生産ラインへのサービス水準を高め、ライン作業の効率化に貢献させる。
正解は・・・
それでは答えです。
「③ 物流工数には手をつけず、生産ラインへのサービス水準を高め、ライン作業の効率化に貢献させる」ことが正解です。
①や②を選ばれた方も多かったのではないでしょうか。確かにこれらも物流改善を進めるにあたり必要な手法です。
しかし、物流改善には順番があるのです。初めて物流改善に取り組む際には、まず生産ラインの徹底した効率化に寄与することが重要となります。
なぜこれが重要なのでしょうか。その理由を、確認していきましょう。
構内物流の仕事
構内物流は、工場内物流、場内物流、マテハンとも呼ばれます。本講座では、構内物流と呼ぶことにします。構内物流の仕事を確認しましょう。
- モノの入庫、保管、出庫
- モノの運搬、ライン供給
- 出荷のための荷揃え、準備
- 容器管理、物流機器管理
- 在庫管理、生産管理、出荷管理、納入管理
これらのことが、物流管理の仕事の主なものになり、一言で表すと、「工場の運営を円滑に進めるために、工場内に“モノ”と“情報”を届ける仕事」と言えます。
構内物流改善の実態
首を傾げたくなる事例が多数・・・
それでは次に、「構内物流改善の実態」について確認します。
実は、工場における構内物流改善では、首を傾げたくなる事例が多数存在します。
一昔前と比べると、物流作業者の少人数化等、「物流を行う側」は効率化されている会社が多くあります。
しかし、その影響が悪い形で生産ラインに出てしまっているケースが多々あるのです。
間違った物流効率化の影響
あなたの工場では、物流自体が効率化された結果、次のような「悪さ」が生産ラインに現れてはいないか、一緒に確認してみましょう。
- ラインサイドに仮置きされた資材を、ライン作業者が生産を中断してラインに投入している
- ライン作業者が資材を容器から取り出す時に、梱包材を取り除く手間が掛かっている
- 今必要ではない種類の資材がラインに供給されており、取出し時に「迷い」が発生している
- 今必要ではない数量の資材がラインに供給されており、つくり過ぎの要因になっている
- ライン内に溜まった空容器を、ライン作業者が生産を中断してライン外へ搬出している
- ラインに届けられた折り畳んだままの完成品容器を、ライン作業者が生産を中断して組み立てている
- 資材や完成品容器がタイムリーに供給されず、生産が中断しライン作業者の手待ちを発生させている
いかがでしょうか。思い当たる節があったのではないでしょうか。
このような状態が発生しているのであれば、あなたの工場では、正しい構内物流改善が行なわれていません。今一度、正しい構内物流改善の進め方を押さえていきましょう。


構内物流が果たすべき3つの役割
構内物流の役割は?
それでは、「構内物流の果たすべき3つの役割」を確認します。
実は、工場の管理者に構内物流の役割は何かと質問すると、「地点から地点へとモノを運搬する運送業」である、という回答が返ってくることがあります。
残念ながら、これは、非常に狭いスコープでの構内物流にしか過ぎません。
物流=運搬という固定観念にとらわれ、仕事の領域を狭めてしまっている会社があまりにも多いのが実情です。構内物流はもっと幅広く仕事をさせるべきものなのです。
それでは、構内物流を考える上で重要な、3つの役割を押さえておきましょう。
サービス業としての役割
構内物流が果たすべき1つ目は、「サービス業としての役割」です。
工場は、ものづくりをすることで価値を生みます。従って、生産ラインがそのものづくりに集中し、極限まで生産性と品質を向上できる環境の整備が必要です。
そうです。つまり、生産ラインの付加価値向上に寄与することこそが、構内物流の本来の役割なのです。
生産ラインのあるべき姿
では、その機能を果たすために、構内物流としてどのような仕事をしていくべきでしょうか。
これを明確化するために、生産ラインの「あるべき姿」を考えてみましょう。
生産ラインはモノを加工することによって付加価値を生み出すので、ムダを排除することが付加価値を高めることになります。
つまり、生産ラインでは、作業者はモノを取って機械にセットし、起動をかけ、加工完了品を指定場所に置く、という動作に特化することが、“あるべき姿”なのです。
実際には・・・
しかし、実際には、この単純な一連の動作の中にも、さまざまなムダが含まれているのです。
例えば、ラインサイドに供給された複数の資材の中から今必要なものを探す動作、これはムダの一種です。
容器から取り出す動作に手間取ってしまっても、ムダが発生していることになります。
また、空になった容器を置き場に持って行き、戻ってくる動作や、加工完了品を入れる容器を手元に引き寄せる動作にも、ムダが含まれています。
さらに、機械から完成品を取り出して整列させながら容器に入れたり、その容器を完成品置き場まで持って行く動作も、広い視点で見るとムダの一種となります。
構内物流=サービス業
このようなムダの発生により、生産ラインの作業者の価値作業である“加工”は、全体の3割に過ぎない工場も数多く存在するのです。
今回の例で構内物流がすべきこととしては、「資材を生産ラインが使いやすいように生産順に供給」し、「完成品や空容器をタイムリーに回収する」ことで、作業者が価値作業に集中出来る環境を作り上げることになります。
構内物流にとって生産ラインは最大のお客様です。そのお客様が喜ぶような商品を提供することこそが最大の役割です。
構内物流は、サービス業であることを、今一度しっかりと認識するようにしましょう。
司令塔としての役割
構内物流が果たすべき2つ目は、「司令塔としての役割」です。
このことの重要性は、誰しも感覚的にはわかってはいても、実際にその役割を正しく理解し実行できていないのではないでしょうか。構内物流は、工場内の血管として、工場内に栄養分を行き渡らせる役割を果たさなければいけません。
つまり、途中で詰まったり、流れが悪くなることなく、必要な時、必要な場所に、必要な分だけ、淀みなく流れるようにすることが、構内物流の第2の役割なのです。
効率的物流を実施する役割
構内物流が果たすべき3つ目は、「効率的物流を実施する役割」です。
まずは、工場内でモノの移動を極力発生させないように、工程を工夫していく必要があります。モノの移動が無い理想状態を目指していきましょう。
また、どうしても工場内でモノの移動が発生してしまう場合には、それを極力効率的に運べないか考えることが大切です。
以上のような物流作業改善は、IE,インダストリアルエンジニアリングの視点を使って、改善を進めていきましょう。
正しいステップで構内物流改善活動に取り組む
以上の3つが構内物流が果たすべき3つの役割となります。
これら3つの役割をベースとして、正しいステップで構内物流改善活動に取り組むことで、会社全体の収益向上に貢献することが可能となります。
それでは以降は、構内物流が果たすべき「3つの役割」は、具体的にどのような形で向上させていくのかを学習していきます。


構内物流改善のステップ
①サービス業として現場の価値時間を向上させる
それでは早速、「構内物流改善の3つのステップ」を確認しましょう。
構内物流改善の初めのステップは、第1の役割として、「サービス業として現場の価値時間を向上させる」活動です。
現場で主役が演技のことを100%考えられるように、構内物流が関係するムダ時間を徹底的に排除していくことが重要となります。
②司令塔として生産の流れをコントロールする
そして、次のステップは、第2の役割として、「司令塔として生産の流れをコントロールする」活動です。
生産指示・出荷指示機能を持つことで、工場のペースメーカーになると共に、工場の司令塔として、モノと情報がスムーズに流れるようにコントロールしていくことが重要になります。
モノと情報が上手くコントロールされ、工場内が淀みなく流れていくために必要な仕組みづくりを徹底的に行なっていきます。
③物流作業を効率化させ物流コストを下げる
最後の3つ目のステップでは、第3の役割として、「物流作業を効率化させ物流コストを下げる」活動です。
工場内でモノの移動を極力発生させないような工程の工夫や、工場内で発生したモノの移動を極力効率的に実施する等、物流自体の効率化を推進していきます。
以上の、HOP、STEP、JUMPの3つのステップで物流改善を進め、生産ラインの生産性向上への寄与と物流コスト低減を推進していきましょう。
改善の前に ~ムダ排除の考え方~
前工程に掃き出す
それではここからは、構内物流改善を進めていくにあたって必要な知識・考え方を押さえておきましょう。
まずは、ムダ排除の考え方からです。「ムダは前工程に掃き出す」ことが基本です。
後工程から前工程に、そして、前工程から前々工程へと掃きだしていきましょう。
一箇所に集め目立たせる
そうすることで、ムダを一箇所に集め、目立たせることができます。
個々のムダを個別最適で改善してしまうと、後工程でデメリットが発生したり、状況によって上手くいかなかったりといったような問題が発生します。
そこで、前工程、前工程へと一箇所にムダを集め、そこに集められたムダに対して改善を行なうことで、全体最適かつ効率的な改善を行なうことが可能となることを覚えておきましょう。
改善の前に ~隠れたムダを“おもてか”する~
表化!(おもてか)
次に、「隠れたムダを“おもてか”する」ことの重要性を確認します。
現場で行なっている作業には、実は物流に関係するムダが隠れています。
初期の段階で、その隠れたムダを表化(おもてか)することが必要不可欠です。
例えば、部品選びや、箱引き寄せ、部品向き替え、梱包材外し、歩行、箱片付け等の動作は、普段は意外と気付かない隠れたムダです。
一連の動作を分析しながら、こういった隠れたムダを1つずつ表化(おもてか)していきましょう。
改善の前に ~生産ラインの実態把握~
生産ラインの実態を調べてみよう!
次に、「生産ラインの実態把握」についてです。
価値作業とは、組立工程であれば、部品を取って取り付ける動作のみを指します。
生産ラインにおける作業では、価値作業にどのくらい特化出来ているでしょうか。また、価値作業以外の作業は、どのくらいの割合で発生しているでしょうか。
改善前に、これらの実態を正しく把握しておく必要があります。
調査に当たっては、稼働分析を活用して行ないましょう。
稼働分析とは
稼働分析とは、一定期間の生産活動の中で、人や機械がどのような要素にどれだけの時間を掛けているかを明らかにするための手法のことです。
「人の働きがどのような状況か掴み」、「改善の切り口を見つけ」、「改善前後の時系列的な変化をつかむ」ために有効なツールです。
一般的に、稼働分析では、主体作業、付随作業、ムダの3つの要素がどのくらいの割合を占めているかを数値で把握することが可能です。
さらに、主体作業の中でも価値作業と呼ばれているものがあり、直接利益を出している、付加価値に繋がる作業のことです。実際に、形状・性質等、物を変化させている作業が該当します。
付随作業は、完全にムダではないが、付加価値に直結しない作業のことです。ムダは、付加価値に結びつかないすぐにでも削減すべき作業のことです。
実際に稼働分析をしてみると・・・
こちらの円グラフは、ある会社の組立工程で稼働分析を行なった結果を示したものです。
組み付け、部品取り、製品格納、部品入れ替え、製品検査、空容器処理、歩行、伸び上がり、ラベル貼付け、絡みほぐし、迷い動作、という分類で調査したところ、主体作業は4割に満たないことが分かりました。
更に、価値作業という視点では、2割にしか満たないということも明らかになりました。ここで、主体作業以外の動作を見てみましょう。
例えば、歩行や伸び上がりが多いのは、構内物流担当者による部品の置き方、場所が悪い為に発生します。また、絡みほぐしや迷い動作が発生してしまうのも、現場作業者の作業のことを考えた部品供給が出来ていないことが要因です。
この比率では、とても合格点はあげられません。最低でも7割超えを目指していくことが必要不可欠です。
このように、実際に稼働分析をしてみると、普段着目していないムダが見えてきたり、思ってもいない意外な結果が出てくることも多々あります。構内物流改善を進める際には、まずは現状の実態をしっかりと把握し、改善を行なっていく過程で、その数値がどう変化しているかを定量的に分析していきましょう。
改善の前に ~理想的な部品の渡し方~
極限まで生産性を上げるために
次に、生産ラインへの「理想的な部品の渡し方」についてです。
生産ラインが、価値作業に特化することで、極限まで生産性を上げるためには、構内物流として、部品の渡し方も理想に近づけていかなければなりません。部品の渡し方は、タイムリーに、使う順番で、今必要な種類の部品だけを、今必要な数だけ、すぐに使える状態で、渡すのが理想です。
この渡し方を理想として、構内物流改善のステップを1歩ずつ進めて近づけていきましょう。


構内物流のまとめ
以上で学んだことをまとめてみましょう。
構内物流の役割とは?
- 構内物流は、工場の運営を円滑に進めるために、工場内に“モノ”と“情報”を届ける仕事
- 物流を行う側だけが効率化され、その影響が悪い形で生産ラインに出てしまってはいけない
- 本来の役割を果たせていない構内物流組織になっていないかしっかり考える必要がある
- 構内物流が果たすべき3つの役割とは、サービス業としての役割、司令塔としての役割、効率的物流を実施する役割
構内物流のステップとは?
- 構内物流は、「HOP:サービス業として現場の価値時間を向上させる」「STEP:司令塔として生産の流れをコントロールする」「JUMP:物流作業を効率化させ物流コストを下げる」
- ムダの排除は、前工程に掃き出し、一箇所に集め目立たせるという考え方で進めていく
- 各工程だけで個別に最適化を行なうのではなく、全体最適で改善を進めていくことが大切
- 生産ラインへの理想的な部品の渡し方は、タイムリーに、使う順番で、今必要な種類の部品だけを、今必要な数だけ、すぐに使える状態で渡す形
いかがでしたか?本ページでは、構内物流の機能や役割、考え方などについて解説しました。
構内物流というと、単なる運搬だと思っていませんでしたか?工場の中のサービス業として、より現場の価値を上げられる構内物流を目指していきたいですね!


関連学習動画
-
k2-14
アニメで学ぶIE実践編~稼働分析 Part1~
有料サービス限定
Lesson3:連続観測法
受講対象者
係長向け,次長・課長向け- カリキュラム構成
-
- 連続観測法とは
- 連続観測法の手順
- まとめ
-
i-004
【法人コース一部お試し】時間研究の考え方と活用法
公開講座
第3章以降は、法人向けサービスで限定公開中!
受講対象者
生産部門、間接部門全般(中堅/管理職)- カリキュラム構成
-
時間研究の考え方と活用法
第1章:時間研究の概要
第2章:レーティングの考え方と評価方法
第3章:標準時間の考え方と設定方法 ※法人向け限定
第4章:PTS法(MODAPTS法) ※法人向け限定
-
k-006
【法人コース一部お試し】ロスゼロ必達!TPM基礎講座
無料会員限定
第2章a:ロスの考え方と管理方法
受講対象者
生産部門全般(一般/中堅/管理職)- カリキュラム構成
-
- はじめに
- 目次
- 設備7大ロスと管理指標
- 指標計算の練習をしよう!
- 前編まとめ
-
k2-04
アニメで学ぶ”5S活動~5Sの概要と整理整頓編~”
有料サービス限定
3:5Sによる効率の向上
受講対象者
現場部門, 間接部門, 新人, 一般, 主任・班長クラス, 係長クラス, 課長クラス- カリキュラム構成
-
- 5Sによる効率の向上とは
- 整理整頓ゲームで効果を確認
- モノ探しの年間ロスコスト
- まとめ
-
k2-14
アニメで学ぶIE実践編~稼働分析 Part1~
公開講座
Lesson1:稼働分析とは
受講対象者
係長向け,次長・課長向け- カリキュラム構成
-
- はじめに
- 稼働分析とは
- 稼働分析の狙い
- 稼働分析の代表的な手法
- まとめ
-
k-006
【法人コース一部お試し】ロスゼロ必達!TPM基礎講座
公開講座
第1章:TPMの概要
受講対象者
生産部門全般(一般/中堅/管理職)- カリキュラム構成
-
- はじめに
- 目次
- TPMの定義
- TPM活動の3つのパート
- TPMの基本理念
- 生産活動における16大ロス
- TPMの8本柱
- TPMとTPS
- 第1章まとめ