標準化とは?バラツキをなくし生産性を上げるための標準化の考え方
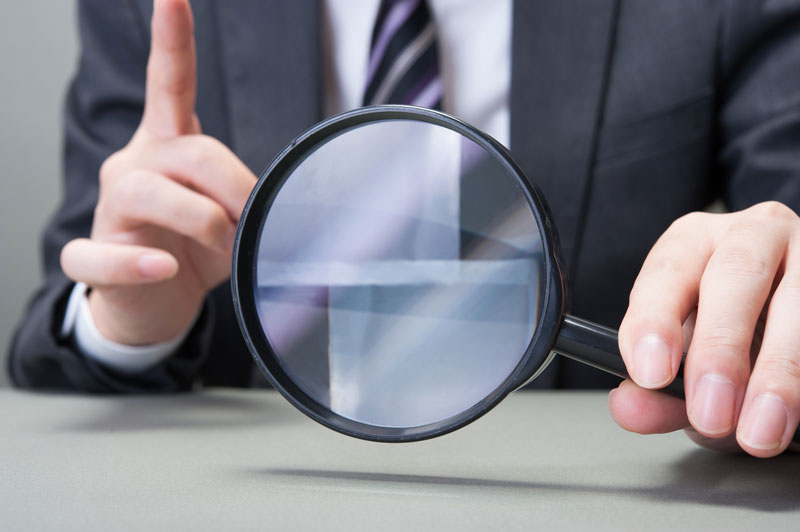


標準化とは?
本ページでは、バラツキをなくし、高い生産性、短いリードタイムで生産活動を行うために非常に重要な「標準化」の考え方について解説しています。
標準化とは
誰でもその方法に沿って作業や業務を行なうことが出来る
標準化とは、その時点で最も優れた方法を定め、誰でもその方法に沿って作業や業務を行なうことが出来るようにすることを指します。
普段、複数の関係者で仕事をする際、各々に好き勝手な方法を取ると、結果もバラツキが大きくなってしまいます。つまり、品質悪化や効率悪化に繋がってしまうのです。
従って、現場作業だけではなく、間接業務等も含めて、仕事を「標準化」することが大切となります。標準化をすることで、仕事の成果のバラツキが小さくなり、いつもしっかりとしたアウトプットが出せるようになるのです。
様々な規格の種類
標準化と一言で言っても、様々な視点があります。
例えば、標準化の代表例である「規格」の種類には、ここに挙げているだけでもたくさんあります。まずは、国際規格、地域規格、国家規格、団体規格などです。
これらの規格では、基本的に製品やサービスの利用者の利便性を考えて制定されています。例えば、複数の設備を導入する際、入ってきた設備の仕様が全く異なるもので、使用している部品や使い勝手がバラバラだったらどうでしょうか?
それらの設備を使用するユーザー側に取ってみると、非常に使いづらく、余計なコストも掛かってしまいます。そういうような利用者の視点から見ても、標準化の1つである「規格」というものは大切なものなのです。
なお、社内規格では、事業所間の統一性や、安全で高い生産性を維持するための作業標準等があります。
以上のように、「規格」をはじめとして、世の中には様々な標準化が行なわれているのです。


標準化の目的とメリット
標準化の目的
標準化が出来ていないと発生する問題
では次に、標準化の目的について確認しましょう。
標準化が出来ていないと発生する問題には、様々あります。例えば、次のようなものが挙げられます。
- 仕事を行う度に結果(製品品質、業務精度等)がバラツいてしまうこと
- 人が違うと結果(製品品質、業務精度等)がバラツいてしまうこと
- 結果的に、時間のムダや損失発生等が生じてしまうこと
製造現場での作業の例を挙げてみましょう。
例えば、Aさんが1個組立を行なうのに60秒掛かるとします。一方で、Bさんが組立をすると45秒で行なえる場合、1日300個組立を行なった際には、どのくらいの差が発生するでしょうか。
計算をしてみると、Aさんの場合は5時間掛かり、Bさんの場合は3.8時間で終わることになります。1個当たり15秒だけの違いだったとしても、1日を通して考えると、大きなロスが発生することになるのです。
標準化をしなくても、仕事を進めることはできます。
しかし、作業の違いをそのまま放置してしまうと、生産性への影響が出てしまいます。品質においても同様です。作業の違いによって、不良率の違いが発生すると、不良ロスが発生することになります。
本来防げるロスを防げずに、お金を無駄にしてしまうのは、非常にもったいないことですよね。これが標準化が必要な一番の理由なのです。
標準化のメリット
以上を踏まえ、標準化のメリットについて確認していきます。
安定したバラツキのない製品づくり
まず1つ目は、安定したバラツキのない製品づくりです。
バラツキの少ない製品の品質を向上させるためには、生産プロセスにおける4M(人、機械、材料、方法)の変化点管理が必要です。標準化により、人、機械、材料、方法の変化点管理が確実なものとなり、生産プロセスのレベルが向上します。
生産性向上とコスト低減
2つ目は、生産性向上とコスト低減です。
標準化によりムダを無くし、高効率な作業や業務を行なうことにより、低コスト体質が構築され、ポカミスやヒューマンエラーを減らすことにも繋がります。
なお、コスト低減においては、様々なムダを削減することに加えて、部品・材料の種類を減らすことも必要です。部品・材料の種類を減らすことができれば、置き場や運搬等、スペースや作業も低減することが可能となります。
そして、部品の互換性を持たせることにより、設計・修理などにおいても大幅なコスト削減に繋がるのです。
リードタイムの短縮
3つ目は、リードタイムの短縮です。
標準化により手直しや手戻りが無くなれば、直行率が向上します。
直行率とは、どのくらい手直しや手戻りなく製品やサービスをつくることが出来たかを表す指標です。手直しや手戻りが無くなった結果、短いリードタイムでお客様へ製品やサービスを提供することが出来るようになります。
つまり、より早くお客様へ製品やサービスをお渡しすることが出来るのです。
標準化で得られるその他のメリット
その他にも標準化で得られるメリットがあります。
技術の蓄積という視点では、個人が習得した固有技術を、企業としての技術として蓄積することが出来ます。技術力の向上という意味でも、蓄積された技術が基礎となり、より技術力を高めることに繋がります。
また、部門間連携の強化という視点では、標準化により、会社として仕事の進め方が統一できるため、部門間の連携が良くなるというメリットがあります。担当者によって、仕事の進め方が異なっている状態では、部門間での調整業務も多大になります。仕事のプロセスを標準化することにより、最低限の調整業務で仕事を行うことが出来るのです。
そして、育成訓練期間の短縮という視点も外せません。仕事の進め方を標準化することができれば、仕事を覚えるのがより容易になります。その結果、教育時間も今までより短くすることが可能となるのです。
以上のように、標準化により得られるメリットはたくさんあります。いかに作業や業務のプロセスを標準化出来ているかが、その会社の仕事の水準を左右していると言っても過言ではありません。それくらい標準化は大切であることを、しっかりと理解しておくようにしましょう。
標準化のポイントと留意事項
標準化のサイクル
まずは、標準化のポイントとして、標準化のサイクルについて確認します。
標準化のサイクルにおいては、次の3つを回していくことになります。
- 全員の知見を集約し、標準をつくる
- 全員に周知徹底し、標準を守る
- 現状に甘んじずに、標準を発展させる
当然ながら、標準をつくるだけではいけません。標準をつくるだけではなく、守り、発展させるサイクルを回し続けることが第一のポイントです。
標準化に必要な4つの基本条件
そして、標準化に必要な4つの基本条件というものがあります。
- 誰でも実行できること
- 誰にでも分かり易いこと
- 誰でも守れること
- 常に改善され続けていること
これらの条件が揃っていなければ、その標準は形式的なもの、あるいは効果のないものになっている可能性があることを認識しておかなければいけません。
標準を誰もが守れるようにするために
特に、誰でも守れる標準をつくることは重要です。
誰でも守れるようにするためには、標準の文書化だけではいけません。
文書化に加えて、「なぜその方法で作業することが重要なのか」、しっかりと理由を理解し、実際に出来るまで訓練をすることが必要不可欠となります。
標準化において失敗しがちなこと
ここで、よくある標準化の失敗例と留意点について確認しておきましょう。
守れない標準を作ってしまう
1つ目は、守れない標準を作ってしまうことです。
よく聞く標準化に対する意見として、「その標準は使えない」「標準が守られない」といった問題があります。
これらは、先ほど挙げた「標準化が備えるべき4つの基本条件」を満たしていないために起こります。
- 実際に標準を守る作業者自身がその標準づくりに参加出来ていない
- 現場監督者が机上で考えただけで、実際に守る立場の人の考えを無視した標準になっている
- 標準化のための標準化となってしまっている
これらが原因として挙げられます。このようにして出来上がった標準は、守れない・守られないものになってしまうのです。
標準を一度作って終わりにしてしまう
2つ目は、標準を一度作って終わりにしてしまうことです。
標準は常に未完成と考えるべきものです。維持しながら改善を行ない、標準を常に改定し続けることが大切です。
標準化するからこそ、問題が見え易い環境を作ることが出来ます。そして、意図的に問題を見える化するからこそ、技能や技術力を向上させ易い職場環境になることを認識しておく必要があるのです。
標準化は作業だけだと思っている
3つ目は、標準化は作業だけだと思っていることです。
標準化が現場の作業だけと考えるのは間違いです。スタッフ業務等の間接業務でも考え方のプロセスを標準化することが可能です。
たとえ、仕事の内容が毎回変化するとしても、必ず仕事の進め方には共通点があり、そのプロセスは標準化を進めていく必要があるのです。
実務で使える標準化を目指そう!
以上で説明したように、作業手順や業務手順等の標準をつくり、守り、そして改善し続ける一連のプロセスが標準化であることは理解出来ましたよね?
標準化の推進によって、品質の向上、作業の効率化、コスト低減、ヒューマンエラーの防止、技術力の向上、コミュニケーションの活性化に必ず繋がります。
審査や監査の時だけの形だけのものにせず、実務で使える標準化を是非とも目指していきましょう!


標準化のまとめ
以上で学んだことをまとめてみましょう。
標準化とは?
- 標準化とは、その時点で最も優れた方法を定め、誰でもその方法に沿って作業や業務を行なうことが出来るようにすること
- 標準化の3つのサイクルとは、標準をつくること、標準を守ること、標準を発展させること
- 標準をつくるだけではなく、標準を守り、そして発展させていくことまで含めて標準化であることを覚えておくことが大切
- 標準化に必要な4つの基本条件とは、誰でも実行できること、誰にでも分かり易いこと、誰でも守れること、常に改善されていること
いかがでしたか?標準化の考え方はイメージできましたか?
作業手順や業務手順をただ作るだけではなく、バラツキをなくし、生産性やリードタイムのレベルを上げることができる標準化を目指していきたいですね!


関連学習動画
-
k2-13
アニメで学ぶ“IE実践編~時間研究 Part2~”
公開講座
Lesson1:標準時間はなぜ必要?
受講対象者
係長向け,次長・課長向け- カリキュラム構成
-
- 標準時間はなぜ必要?
- 標準化の目的とメリット
- 標準時間運用のサイクル
- まとめ
-
k2-15
アニメで学ぶIE実践編~稼働分析 Part2~
有料サービス限定
Lesson3:ワークサンプリング“実施・分析フェーズ”
受講対象者
係長向け,次長・課長向け- カリキュラム構成
-
- ⑦のポイント
- ⑧のポイント
- ⑨の概要
- まとめ
-
k-012
リーダーが知っておくべき生産現場管理の基本
有料サービス限定
3:1個流しの重要性(組付編)
受講対象者
現場部門, 主任・班長クラス, 係長クラス, 課長クラス- カリキュラム構成
-
- 1個流しが出来ていないと起こる問題
- 1個流しの必要性まとめ
- まとめ
-
k2-11
アニメで学ぶ“IE実践編~動作研究 Part2~”
無料会員限定
Lesson2:両手作業分析とは
受講対象者
係長向け,次長・課長向け- カリキュラム構成
-
- 両手作業分析とは
- 両手作業分析の4区分
- まとめ
-
k2-18
アニメで学ぶIE実践編~応用手法 Part1~
有料サービス限定
Lesson3:M-Mチャートの事例
受講対象者
全部門(管理職)- カリキュラム構成
-
- はじめに
- M-Mチャートの事例①
- M-Mチャートの事例②
- M-Mチャートの事例③
- まとめ
-
k2-10
アニメで学ぶ“IE実践編~動作研究 Part1~”
有料サービス限定
Lesson8:動作経済の原則による作業チェック
受講対象者
係長向け,次長・課長向け- カリキュラム構成
-
- 4つの基本原則のおさらい
- チェックシートの活用
- OODAループ
- まとめ