パレート図とは?パレートの法則(80:20の法則)とABC分析の活用法
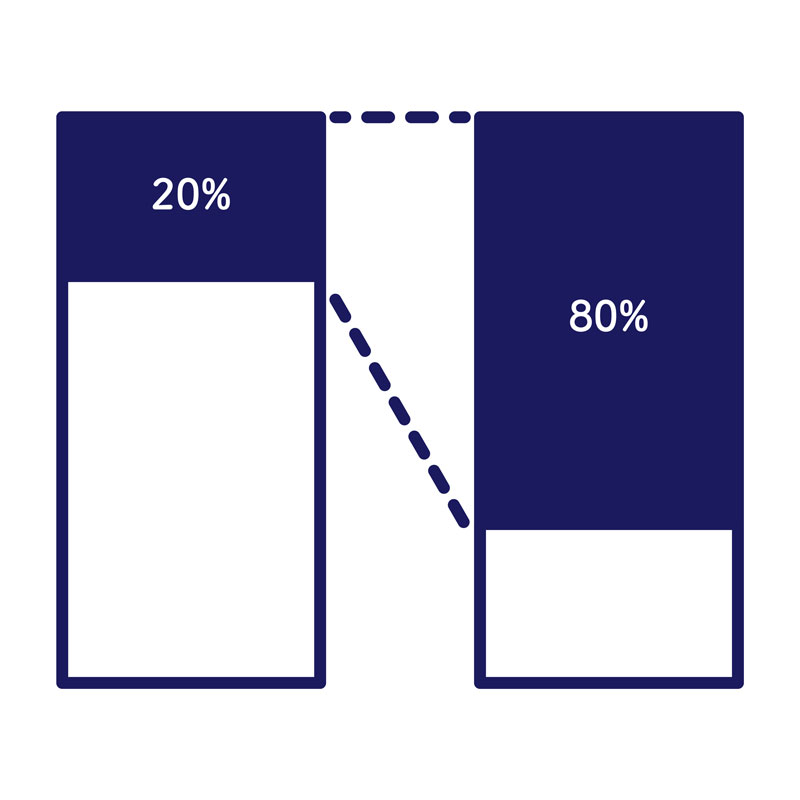


パレート図とは?
パレート図とは、「全体の中で大きな影響を占めるものが何であるかを明確にし、重要な問題を特定するための手法」です。パレート図は、QC7つ道具の1つですが、QCだけではなく、改善活動のあらゆる場面で有効に活用できる手法でもあります。
本ページでは、パレート図を作成する目的やパレート図作成の基本について解説しています。内容を理解し、実務で活用できるようなレベルを目指していきましょう。
パレート図を作成する目的
パレート図の主な使用目的としては、
・重点的に取り組む問題を特定する
・その影響がどの程度か把握する
・改善前と改善後の効果を確認する
等が挙げられます。
パレート図はこのようなイメージで作成します。ここに示しているものは、キズ、割れ、凹み、欠け のように、不良要因別に分類し多い順から並べた例です。
このようなパレート図を描いてみることで、例えば、不良全体の中でキズが85%を占めており、キズを重点的に対策すべきであると容易に特定できるようになります。
つまり、パレート図は、各分類項目の影響度が一目で分かるようになり、どこに重要な問題があるのかを的確に特定するために有効な手段なのです。
もちろん、品質管理だけではなく、あらゆる改善において、重点指向でモノゴトを捉えることは必要不可欠ですよね!
パレートの法則とは
ここで、パレートの法則について確認しておきましょう。パレートの法則とは、上位2割で全体の8割を占めるという経験則です。
仕事において起こるトラブルの原因の20%が、全体の結果の80%を作っているということはよくあることです。裏を返すと、上位20%の原因を潰せば問題の80%が解決するということになります。改善活動においても、時間という資源を最大限有効に使うために、影響が大きいものに重点的に手をかけることが重要です。
パレートの法則が当てはまるものは他にもあり、
・売上の8割は、全顧客の上位2割が占めている。
・売上の8割は、全商品の内の2割の品種によって作られている。
・仕事の成果の8割は、費やした全時間の内の2割の時間で生み出されている。
・故障の8割は、部品の2割に原因がある。
といったようなことが挙げられます。
パレート図の用途
それではパレート図の具体的な様々な用途を見てみてみましょう。
発生件数や発生金額での分類としては、
・不良発生件数や不良発生金額の分析
・クレーム件数やクレーム金額の分析
・設備の故障発生件数や故障発生金額の分析
・製品別の在庫個数や在庫金額の分析
等が挙げられます。
原因別での分類としては、
・不良発生原因別の分析
・クレーム発生原因別の分析
・故障発生原因別の分析
・在庫発生原因別の分析
等が挙げられます。
現象面だけでなく、原因別で分類すると、解決の糸口が掴めることもありますよね。
これらのような視点も踏まえ、どんな分類で分析を行なうと効果的か、しっかり考えた上でパレート図を作成するようにしましょう。
パレート図による改善効果の表し方
なお、パレート図による改善効果の表し方は、このようなイメージです。
不良の個数低減の取組みをしている場合、改善前の状態に対して、改善後も目盛りを合わせて描くと、減少した不良個数分、パレート図が小さくなります。この小さくなった分が改善効果となります。
つまり、改善前と改善後のパレート図は、縦軸の目盛りを同じにすることによって、効果の大きさを視覚的に表すことが可能になるのです。


パレート図の作成方法
それでは次に、パレート図の作成方法を確認していきましょう。
手順1:データの収集
手順1は、どのようなパレート図を描くか決め、データを収集します。
まずはしっかりと問題のデータを層別し、データの特性値を決めます。
そして実際にデータの収集を行ないます。
手順2:データの整理と表の作成
手順2では、収集したデータを整理し、表を作成します。
このように、パレート図の作成に必要な各種項目をExcel等を使い、表形式にまとめます。
品質改善を行なっており、原因別に調査をしている場合には、「不良項目」「個数」「割合」「累積割合」が必要になりますね。
なお、不良項目・個数の列に関しては、基本的に数が多い順に並べます。
そして、割合の列では、不良個数全体の中のその項目の割合を計算します。
汚れの場合なら、91個/188個となり、48.4%ですね。
この列は全部を足すと必ず100%になります。
累積割合に関しては、順番に累積で足していきます。
割れの場合だと、キズまでの累積80.3%に、割れ単独の割合6.4%を足し、86.7%となります。
この列は最後の項目を足すと必ず100%となります。
手順3:棒グラフの作成
手順3では、棒グラフを作成します。
不良項目と個数を大きい順番に並べて描くだけでOKです。
ただし、「その他」は一番右端でかまいません。
なお、この時点でデータの個数(N数)と、データの期間や担当者等の必要情報を記載しておきましょう。
手順4:折れ線グラフの追加
手順4では、累積割合の折れ線グラフを追加します。
累積割合は第2軸(右軸)に描くこと、0~100%の範囲で書くことがルールです。
なお、折れ線グラフの最初の点は、1番目の項目の棒グラフの右肩に打点するのも、分かり易いパレート図を作成するための決まりごとの1つです。
パレート図活用の際の注意点
それでは続いて、パレート図活用の際の注意点について確認します。
多段展開のし過ぎに注意
1つ目は、多段展開のし過ぎに注意をすることです。
不良発生個数全体のパレート図に対して、項目を何度も細分化し過ぎてしまうと、
始めに捉えていた問題の大きさ全体に対して、分析する対象が小さくなり過ぎてしまいます。
あまりに小さくなり過ぎると、当然得られる効果も小さくなってしまいます。
そのため、取り上げる問題を絞り過ぎていないかしっかり確認することが大切です。
分析期間の設定に注意
もう1つの注意点は、分析対象期間の設定に注意することです。
あまりに長い期間を対象に分析を行なうと、その期間内に工程変更、主力製品のモデルチェンジ、ベテラン作業者の退職など、沢山の変化点がある場合があります。
このように沢山の変化点がある期間を対象にパレート図を描くと、正しい状態を表さないことがあります。
パレート図を作成する場合には、変化点の前後で作成し比較すること、3ヶ月から1年程度の範囲で作成すること等に気を付け、同じ条件で分析を行なうようにしましょう。


パレート図とABC分析
それでは次に、「パレート図とABC分析」について確認しましょう。
ABC分析とは
パレート図はただ作っただけで満足してはいけません。
実務においては、ABC分析により、分析結果に対して、改善の方針を決め、実際に深堀り調査、真因分析、対策を行なっていくことが必要不可欠です。
ABC分析とは、累積比率に対して、Aランクを0~80%、Bランクを81~ 95%、Cランクを96~100%というようにランクを付け、取り組む対象を明確化する手法です。
各ランクの数字は、これを基準として、状況に応じて柔軟に変更を行ないます。
各ランクについて詳しく確認していきましょう。
Aランクの考え方
まずは0~80%のAランク群です。
Aランクは、品種数は少ないが占める割合が大きく、全体への影響度が大きくなります。
従って、改善を行なう際には、最優先で取り組む対象になります。
Bランクの考え方
続いて、81~95%のBランク群です。
Bランク群は、Aランクほど割合は大きくないものの、全体への影響は小さくないため、Aランクを改善した後に取り組む対象となります。
Cランクの考え方
最後に、96~100%のCランク群です。
Cランク群は、全体への影響は小さいため、基本は割り切って後回しにします。
改善を行なう際、影響度を考えずにCランクの製品に対象を決めてしまうと、結果的に得られる効果が小さくなってしまいます。
まずはAランク、その次にBランク、Cランクは対象外にするというように、メリハリを付けた進め方をするようにしましょう。


パレート図・ABC分析のまとめ
以上で学んだことをまとめてみましょう。
パレート図とは?ABC分析とは?
- パレート図とは、全体の中で大きな影響を占めるものが何であるかを明確にし、重要な問題を特定するための手法
- パレートの法則とは、上位2割で全体の8割を占めるという経験則のこと
- 上位20%の原因を潰せば問題の80%が解決することも多く、改善活動では必須の考え方
- パレート図を作成する際の注意事項は、多段展開のし過ぎと、分析対象期間の設定。対象を絞りすぎず、変化点に気を配り分析をすることが大切
- ABC分析とは、累積比率に対しA,B,Cランクを付け、取り組む対象を明確化する手法
- まずはAランクを改善し、その次にBランク、Cランクは対象外にするというように、メリハリを付けた進め方をすることが大切
いかがでしたか?パレート図・ABC分析のポイントはイメージできましたか?
上位20%の原因を潰して問題全体の80%を解決するという重点指向の考え方は、仕事において様々なシーンで求められます。改善活動でも必須の考え方なので、しっかり活用できるようにしていきましょう!


関連学習動画
-
k-014
実務で活用!QC7つ道具の使い方
有料サービス限定
6:散布図とは
受講対象者
生産部門全般(新入社員/一般)- カリキュラム構成
-
- 散布図とは
- 散布図の作り方
- 散布図の見方と考え方
- 散布図活用時の注意事項
- まとめ
-
k-014
実務で活用!QC7つ道具の使い方
有料サービス限定
3:特性要因図とは
受講対象者
生産部門全般(新入社員/一般)- カリキュラム構成
-
- 特性要因図とは
- ブレーンストーミングの5原則
- 特定要因図の考え方と作成手順
- まとめ
-
k-014
実務で活用!QC7つ道具の使い方
有料サービス限定
8:管理図とは
受講対象者
生産部門全般(新入社員/一般)- カリキュラム構成
-
- 管理図とは
- 管理図の見方と考え方
- 管理図の種類
- 管理図の作り方
- まとめ
-
k-014
実務で活用!QC7つ道具の使い方
無料会員限定
2:パレート図とは
受講対象者
生産部門全般(新入社員/一般)- カリキュラム構成
-
- パレート図と重点指向
- パレート図の作成方法
- パレート図活用の際の注意点
- パレート図活用とABC分析
- まとめ
-
k-014
実務で活用!QC7つ道具の使い方
公開講座
1:QC7つ道具とは
受講対象者
生産部門全般(新入社員/一般)- カリキュラム構成
-
- QC7つ道具とは
- 問題解決のステップとQC7つ道具
- QC7つ道具で必要な層別とは
- 漏れなくダブりの無い層別を
- まとめ
-
k-014
実務で活用!QC7つ道具の使い方
有料サービス限定
4:グラフとは
受講対象者
生産部門全般(新入社員/一般)- カリキュラム構成
-
- グラフとは
- 代表的なグラフ~円グラフ・棒グラフ・折れ線グラフ~
- 代表的なグラフ~帯グラフ・レーダーチャート~
- まとめ